Automotive manufacturers are in a race to achieve sustainable mobility and meet "zero emission" targets in development and engineering. Virtual simulation and testing is a powerful approach that enables automakers to reduce the carbon footprint of vehicles and development practices in order to achieve sustainability Key Performance Indicators (KPIs). The use of virtual simulation also contributes to the realization of "vision zero", a world with zero traffic fatalities. By harnessing the digital thread and accelerating digital transformation with Industry 5.0 and Product Lifecycle Management (PLM) applications, automotive engineers can achieve the right balance between accuracy and time-to-market, delivering innovative products at a manageable cost and risk.
How is Virtual Prototyping Empowering Companies to Install Sustainable Engineering Practices, Accelerating the Journey to a Cleaner, Greener, Safer Future?
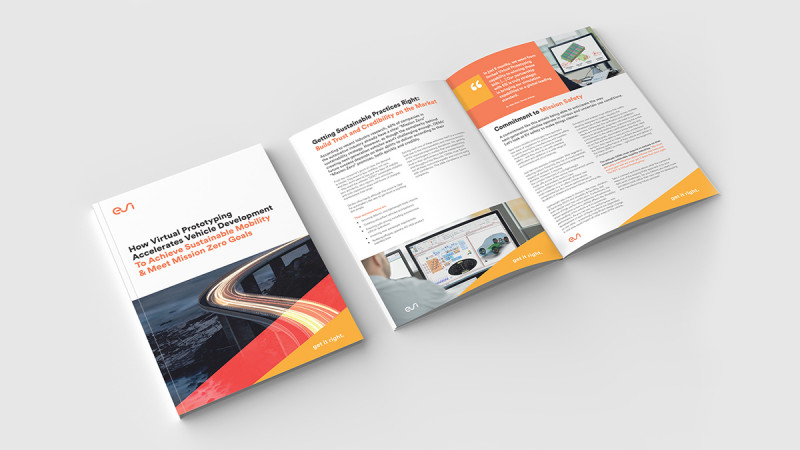
Driven by environmental concerns, government regulations, consumer demand, technological advancements, and corporate responsibility to meet their zero emissions, zero waste, and zero accidents goals, manufacturers of vehicles worldwide are placing sustainability at the top of their agenda.
Eager to learn more? Download the whitepaper and discover the crucial role of virtual prototyping tools for accelerating the engineering development process.
What is the Power of Virtual Prototyping for Automotive R&D?
Discover how virtual testing technology accelerates automakers’ Mission-Zero journey without compromising on quality, safety, or performance; by shifting to virtual vehicle testing you can work smarter, reduce costs, and accelerate time to market.
Virtual Proving Ground for Vehicle Safety & Acoustic Performance
As an engineer, you test and certify new automotive applications entirely virtually with your very own digital automotive test track: emission-friendly, with reduced testing mileage and at the lowest processes, tooling & material cost. Virtual Prototyping allows you to get new designs right the first time while eliminating physical prototype tests for crash studies and sound quality analyses.
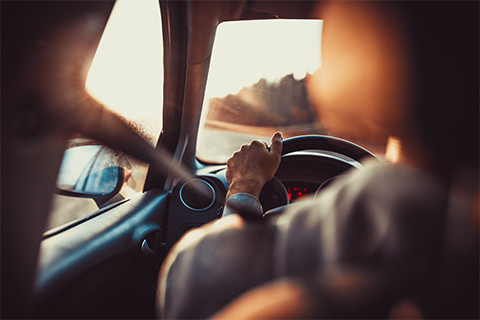
Simulation Software Solutions for Vehicle Safety
Ensure maximum protection for occupants and vulnerable road users and get certification right the first time with only 1 regulatory physical release test before market launch.
Dive deeper into ESI’s simulation solutions for Vehicle Safety
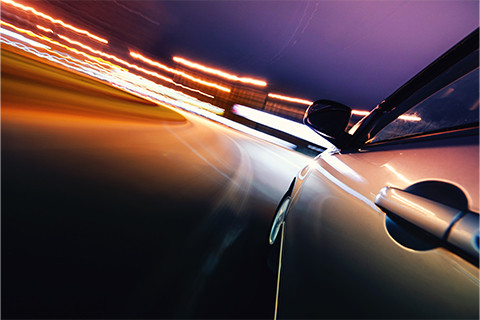
Simulation Software Solutions for Acoustic Performance
Create a pleasant journey with superior sound quality by removing undesired interior & exterior noise using Virtual Prototyping technologies in vehicle design and engineering.
Create a Virtual Process Chain for Vehicle Manufacturing
How can you accelerate the product development cycle? Use the power of Virutal Prototyping to establish concurrent development processes in manufacturing. By frontloading manufacturing engineering and creating a virtual manufacturing process chain, you can decrease lead time and cost for new lightweight designs.
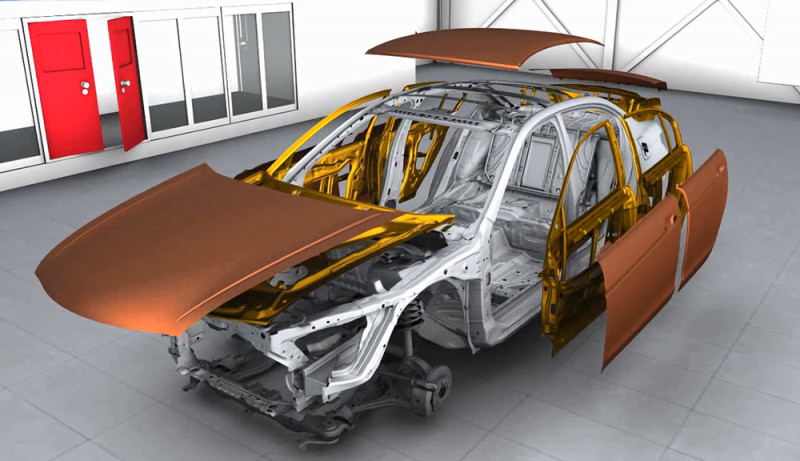
Simulation Software for Body and Chassis Manufacturing
Gain early confidence in the correct materials, manufacturing & assembly processes for new automotive applications before cutting a single piece of metal.
Learn about Simulation Solutions for Body and Chassis Manufacturing
Build your Industrial Metaverse to Power Collaborative Virtual Workflow
Create your own industrial metaverse to experience physical interactions with yet-to-be-realized vehicle designs without waiting for construction or traveling to a common site. Early in the development process, immersively explore new vehicle concepts from a worker and operator perspective and gain a hands-on experience in the processes required to make and maintain them. This is how you push engineering workflows months ahead of production.
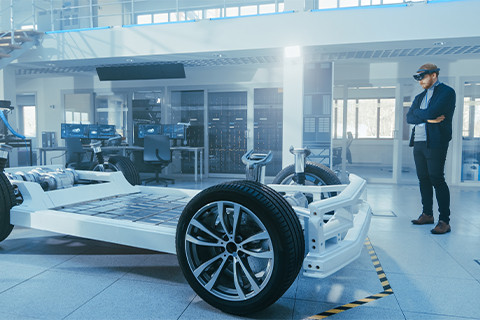
Human-centric Process Validation and Product Integration Using Virtual Reality
Interactive immersive experiences to validate human-performed process validation and complex product integration.
Find out more about our Virtual Reality Solutions for Automakers
Virtual Prototyping in Automotive and Ground Transportation is Trusted By
All over the world, suppliers, manufacturers, and engineering partners use ESI’s solutions to design and optimize future mobility on the ground, e.g. Alstom Transport, Autoliv, Bombardier, Bertrandt, Continental, Daimler, FAW Volkswagen, Faurecia, Fiat/Chrysler, Ford, General Motors, Gestamp, Honda, Hyundai Group, Isuzu, Jaguar Land Rover, MAN, Mazda, Mitsubishi Motors, PSA Peugeot Citroen, Renault Nissan, Shanghai Volkswagen, Takata, Tata Group, Toyota Motor Corp., Visteon, Volkswagen Group, and Volvo Group.