汽车制造商正在竞相实现可持续发展,并在开发和工程中实现 "零排放 "目标。虚拟仿真是一个强大的工具,使汽车制造商能够减少车辆和开发实践的碳足迹,以实现可持续性关键绩效指标(KPI)。虚拟仿真的使用也有助于实现 " vision zero ",即一个零交通死亡事故的世界。通过利用工业5.0和产品生命周期管理(PLM)应用程序的数字主线和加速数字化转型,汽车制造商可以在准确性和上市时间之间实现适当的平衡,以可控的成本和风险交付创新产品。
虚拟样机如何赋能可持续工程研发加速迈向更清洁、更环保、更安全的未来?
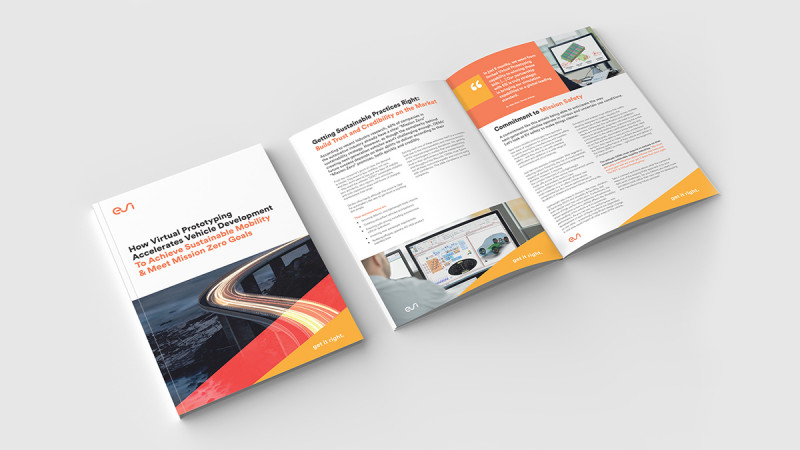
在环境问题、政府法规、消费者需求、技术进步以及企业实现零排放、零浪费和零事故目标的责任推动下,世界各地的汽车制造商正将可持续性置于其议程的首位。观看我们的视频,快速了解虚拟样机在汽车行业的优势。
渴望了解更多?下载白皮书,了解虚拟样机如何加速创新,帮助您实现“Mission Zero”
利用强大的虚拟样机技术推动安全、可持续的创新
了解模拟技术如何在不影响质量、安全或性能的情况下加速汽车制造商的'Mission Zero'之旅;通过将虚拟世界与更安全、更清洁、更高效的现实联系起来,您可以更高效地工作,降低成本,加快产品上市时间。
车辆安全和声学性能的虚拟试验场
使用您自己的数字汽车试验场完全虚拟地测试和认证新的设计:减少测试里程并以最低的工艺、工具和材料成本控制排放。虚拟试验场使您能够在第一时间获得正确的新设计,同时消除碰撞研究和声音质量分析的物理原型测试。
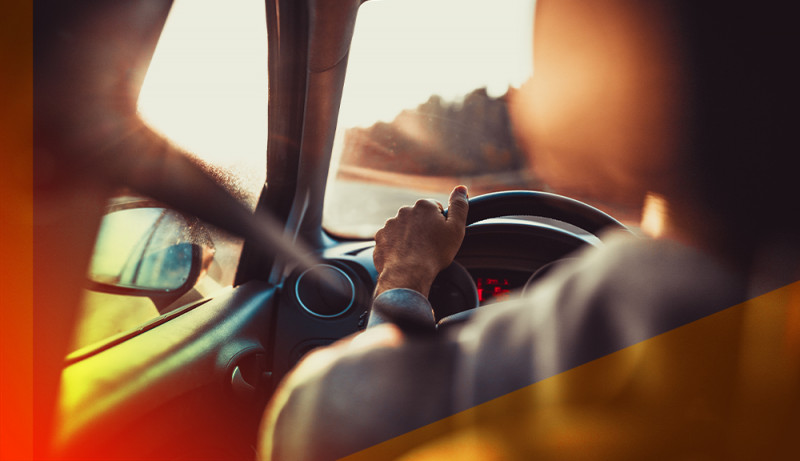
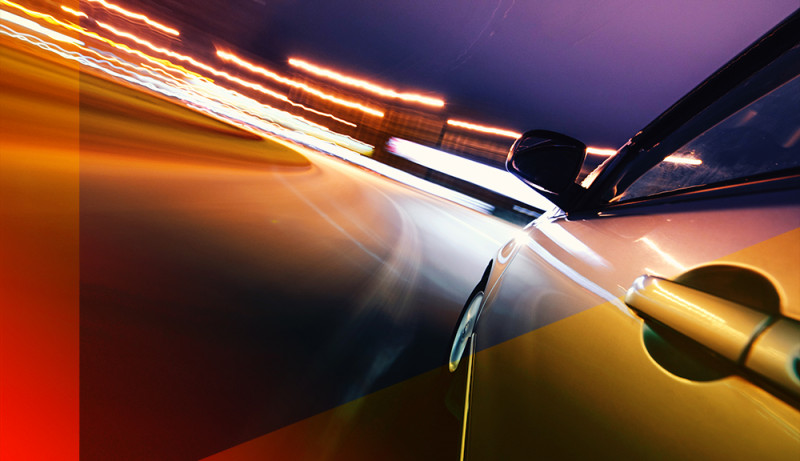
构建您的工业元宇宙,为协作虚拟工作流提供动力
创建您自己的工业元宇宙,体验与尚未实现的车辆设计的物理交互,而无需等待施工或前往实际场景。从工人和操作员的角度沉浸式探索新的车辆概念,并在制造和维护这些概念所需的过程中获得实践经验。这就是您在生产前几个月推动工程工作流程的方式。
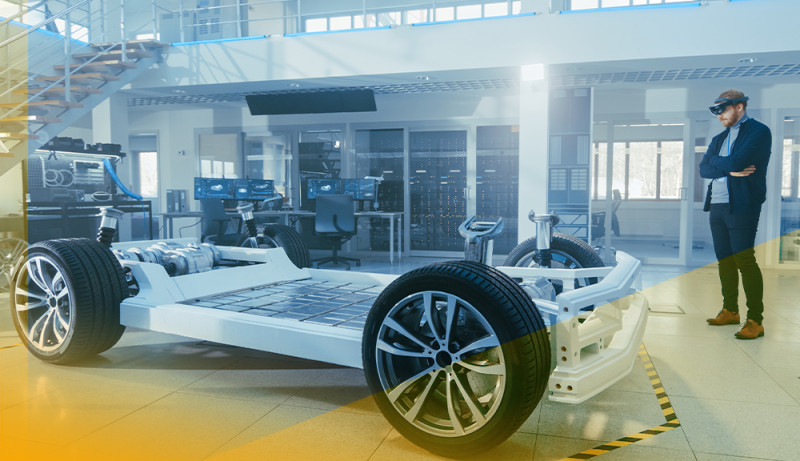
汽车和地面运输中的虚拟样机值得信赖
在世界各地,供应商、制造商和工程合作伙伴都使用ESI的解决方案来设计和优化未来的地面移动产品,例如阿尔斯通运输公司、奥托利夫公司、庞巴迪公司、伯特兰公司、大陆集团、戴姆勒公司、一汽-大众公司、佛吉亚公司、菲亚特/克莱斯勒公司、福特公司、通用汽车公司、盖世坦公司、本田公司、现代集团、五十铃公司、捷豹路虎公司、MAN公司、马自达公司、三菱汽车公司、PSA标致雪铁龙公司,雷诺-日产、上海大众、高田、塔塔集团、丰田汽车公司、伟世通、大众集团和沃尔沃集团。