多材料组件是生产具有合理成本/重量比车身的关键。然而,找到合适的材料组合并将其应用于适当的位置、优化几何形状和厚度、设计稳健的制造工艺和选择更优的连接技术是一个挑战。由于组合的数量几乎是无限的,单点数值模拟不足以完成这项工作。
相反,汽车制造商已经开始转向将工程和制造领域紧密结合起来,以便在开发周期中尽早做出正确的决策,并避免使用昂贵的物理样机进行后期校正。
对于大多数基于钢的车身结构,端到端虚拟样机是OEM的既定方法-从连接产品设计、性能和制造工序。一些关键优势包括:
For most steel-based body structures, end-to-end virtual prototyping is an established approach for OEMs – from connecting the product design, performance, and manufacturing engineering workflows. Some key benefits are:
- Confidence in the best design earlier by predicting manufacturing, assembly and performance through accurate representation of physics and applied processes
- Accurate manufacturing and performance validation of all lightweight materials (standard steel, high-strength steels, aluminum, composites) regardless of what process they have been manufactured through (standard stamping, hotforming, casting)
- Unlimited virtual try-out to find the most efficient manufacturing processes to achieve assemblies with optimal cost/quality ratio ensuring correct performance
- Reduction (and eventually complete elimination) of expensive physical prototypes and time-consuming try-out iterations
Ultimately, end-to-end virtual prototyping is the best way to reduce your overall product development cycle, cost, and time to the start of production (SOP) by getting your sustainable vehicle engineering, manufacturing, and assembly processes right.
Discover the transformative power of ESI's virtual prototyping solutions in revolutionizing car body and chassis manufacturing. This video explores solutions that pave the way for transition from physical to virtual testing, significantly reducing development time and costs, while enhancing vehicle safety and performance.
Watch Mark Vrolijk as he introduces:
- PAM-Stamp: to simulate sheet metal forming and predict issues like cracks in lightweight designs.
- ProCAST: and how to analyze casting processes for quality control.
- PAM-Composites: to model composite materials for strength and lightness.
- SYSWeld: to simulate welding processes to predict quality and distortions.
This video also addresses the challenges of handling high-strength steel, aluminum components, and complex castings before discussing the merits of 'virtual value chains' that connect manufacturing, assembly, and performance for optimal final assembly quality, improved safety, and accelerated time to market.
多材料装配模拟 如何在整个车辆开发周期中为您提供支持
能够在虚拟样机链的早期引入制造信息对产品开发周期的所有阶段都是有益的。
- 产品设计
- 在迭代由具有挑战性的材料制成的零件时,快速提供可靠的可行性分析和材料成本信息
- 性能研发
- 通过包括成形和装配/连接情况,对“制造”(子)组件进行早期碰撞和耐久性/NVH性能分析
- 制造工程开发
- 为寻找更优工艺路线提供有效支持,以期在公差范围内以预期质量交付无缺陷零件(钢、铝、复合材料)
- 装配工程研发
- 开始在实际的部件几何形状上设立装配过程,包括制造过程引起的形变,并确保最终车身或底盘装配在公差范围内
利用虚拟制造仿真软件设计、制造和组装混合材料组件
让我们一起解决制造和装配问题
多年来,ESI一直在与OEM厂商和供应商合作,创建一个端到端的数字线程,将设计、工程、制造、批量生产和维护中的所有不同利益相关者和活动联系在一起。我们陪同客户将其流程从单点、纯数值模拟转变为端到端的虚拟样机——确保他们在第一时间正确完成单个零件的设计、制造和装配流程。这是设计和制造可持续移动设备的多材料解决方案的基础。
从单点数值模拟转移到端到端连接的虚拟样机工作流有什么好处
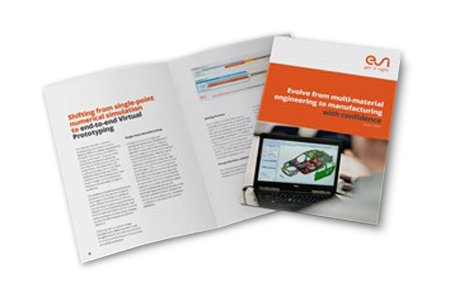
简而言之:快速培养对新材料和制造技术的信心。这一切都是关于在工程范畴内预测制造过程,更早更快地实现优化设计,同时最大限度地减少对物理样机的需求。这使我们的日常工程研发和制造实践更加可持续的关键。
下载白皮书,了解OEM工作流如何从单点数字材料和过程模拟转变为端到端连接的虚拟样机工作流。
Virtual Modeling for Mega Casting
Mega Casting, also known as Giga Casting or Hyper Casting, is a game-changing method for creating large aluminum car parts. It promises a future where cars are lighter and more efficient. But with big innovations come big risks. By simulating every part of the Mega Casting process, you can spot and fix potential problems before spending a lot on tools. This helps optimize designs and ensure smooth production, making the future of car manufacturing much more seamless.
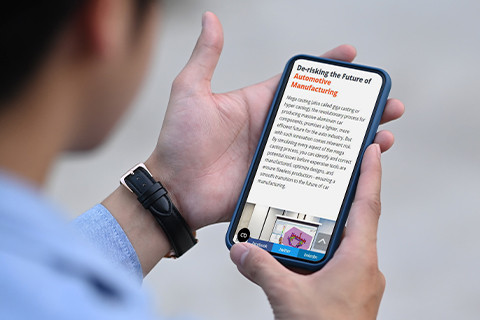