See how ESI's Virtual Prototyping Software Empowers You to Create Safe, Sustainable, and Productive Machines
In heavy industries like construction, agriculture, and mining, manufacturers face challenges in product design, manufacturing, assembly, and operations.
Operators now demand optimal product performance throughout the lifecycle, emphasizing safety and productivity from the initial build to operation and maintenance. The goal is to deliver machinery that's safer, cleaner, and more productive, all while managing costs and meeting lead times through efficient enterprise-wide collaboration, with a commitment to lifetime performance in challenging conditions. This is where Virtual Prototyping comes in, changing the way engineers design and test new products and manufacturing processes by leveraging virtual environments.
Safe & Productive Human-Centric Operations Powered by Virtual Reality
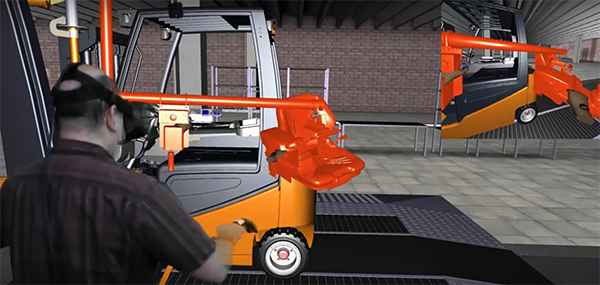
Break the silos between design, manufacturing, and maintenance. Decrease lead times to meet the start of production, at controlled quality and cost. Validate product integration early in a human-centric way. Integrate human interactions at the heart of the factory. Anticipate and optimize human interactions, to protect worker safety and increase productivity while ramping-up production. Develop human-centric maintenance processes early on to secure, speed up and decrease the cost of maintenance. Ensure safe & productive service operations as early as possible.
Virtual Prototyping is Key for Engineers to Beat Expectations
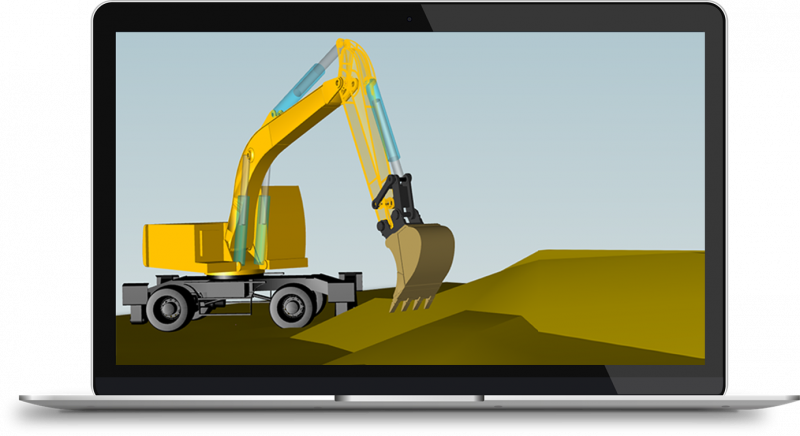
Design for Reality
Get early confidence over product lifetime performance, even for the toughest usage conditions. Catch up with the growing use of mechatronics and complex systems. Implement the latest electrification and automation technologies, by getting clarity on system design, dimensioning, testing and reliability predictions. Anticipate usage faults and misuse scenarios. Plan for operational durability and misuse. Provide fast & safe driving in rough terrains, including vehicle dynamics and stabilization. Investigate dynamic machine behavior, including for emergency stops and shutdown scenarios. Check for tipping safety. Deliver maximum productivity and maximize lifetime usage.
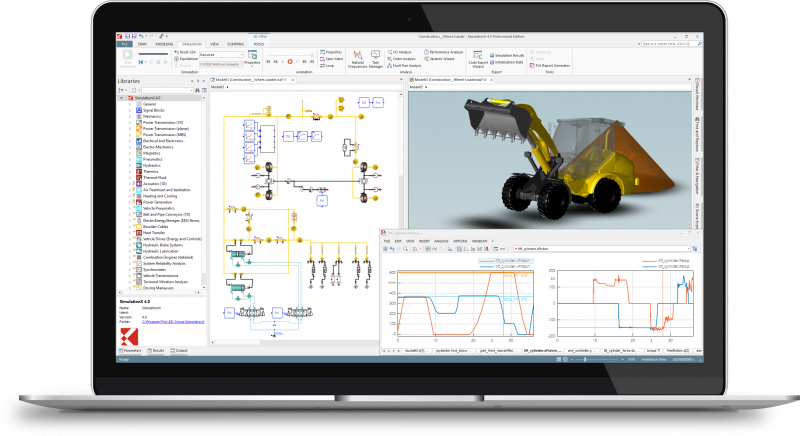
Virtual Proving Ground
Design safe, clean, and productive machinery & equipment. Cut down on real tests and prototypes. Achieve product pre-certification despite constantly evolving regulations. Face challenges related to product performance across multiple domains, from noise and acoustics to durability. Make sure operator safety and comfort are a priority. Evaluate shocks and vibrations experienced by operators at work. Meet regulations and targets for interior and exterior noise & acoustics. Ensure best possible visibility, reachability, accessibility.
What is the Power of Virtual Prototype Simulation Software? Discover the 7 Real Benefits for Heavy Machinery Manufacturers of Emanzipating From Physical Prototyping
Discover how a Virtual Proving Ground, Virtual Manufacturing, and Virtual Collaboration and Validation can help ground vehicle manufacturers accelerate your time to market; improve uptime, safety, and compliance; reduce complexity and costs; and achieve your sustainability goals.
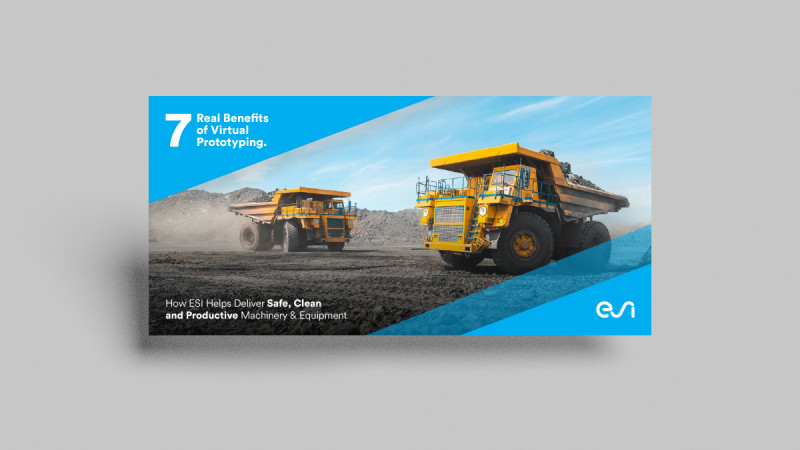
Aim for Zero Defects With Virtual Prototyping
Boost productivity and production output. Improve production ROI by leaning towards zero defects in production. Secure product quality. Model any manufacturing process from casting to sheet metal forming, composites forming, additive manufacturing, welding, joining and assembly. Improve process parameters, even for the most complex product shape and process. Beat your competitors for new business bids, while securing profitability with fast and easy quotes for new tooling and parts production. Skip physical prototypes for new tools, parts, and assemblies. Anticipate and accelerate start of production. Meet requirements and stay within acceptable tolerances. Understand the physics of materials to deliver promised product quality. Say good-bye to scrapping. Improve sustainability aspects for your production plants.
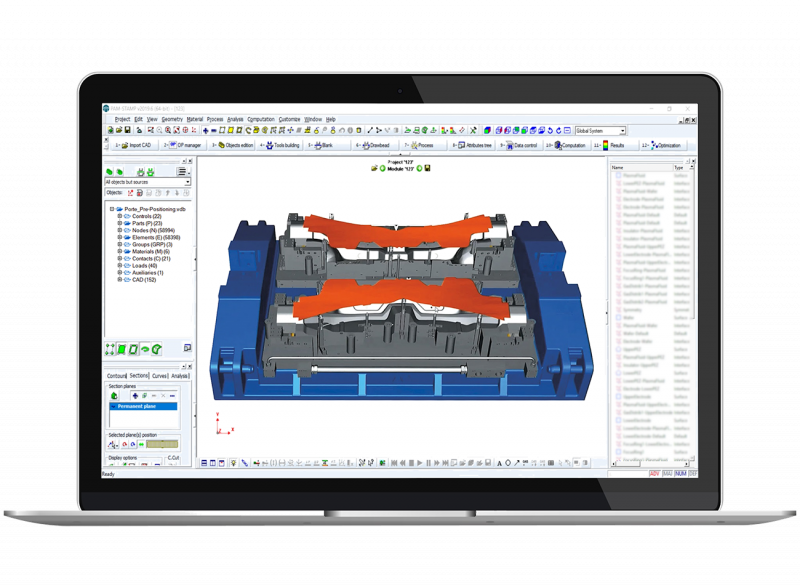
Build on the Hybrid Twin When Aiming for Zero Downtime
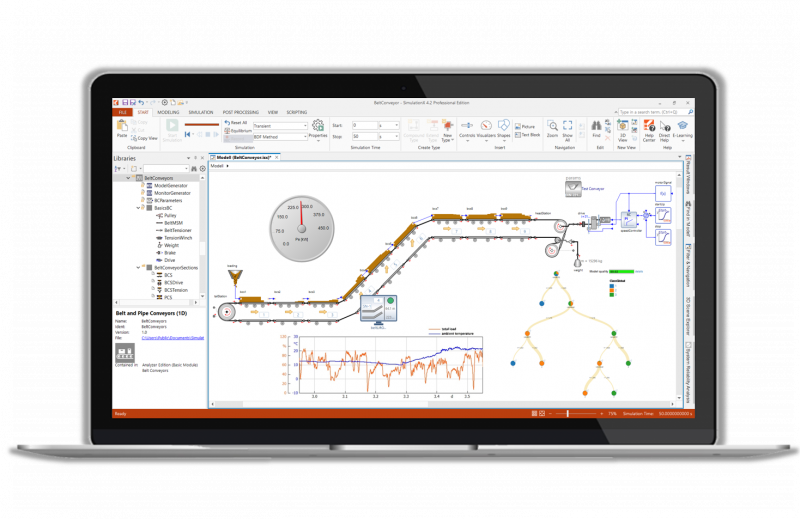
Give your clients maximum uptime. Switch from preventive to predictive maintenance, diagnostics, and prognostics. Expand your mindset: switch from PLM to ESI’s Product Performance Lifecycle. Build your very own Hybrid Twin, leveraging the physics of materials and data gathered from sensors. Make the right decision at the right time to protect your assets.
New eBook: Pioneer Innovation with Virtual Prototyping.
Discover ESI’s virtual proving ground, virtual manufacturing process chain, and collaborative workflow solutions that power the design, test, and manufacture of clean, safe, and productive heavy machinery. Learn how your peer engineers in heavy machinery companies are already reaping the rewards of digital approaches and how ESI's virtual prototype simulation software can help you can innovate without compromise. Get our latest eBook now.
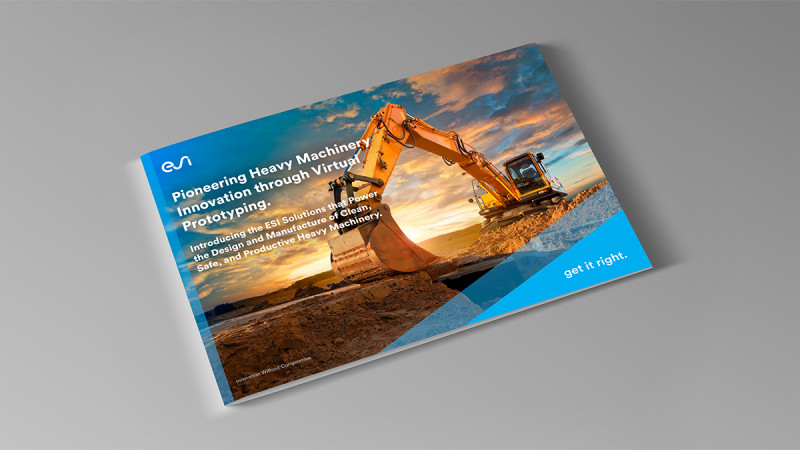
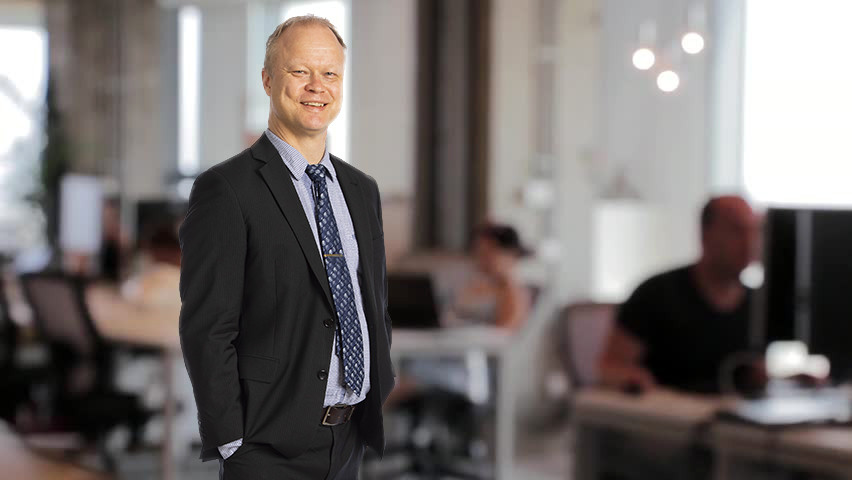
“We accompany you in developing safe and reliable products with production processes that target the highest product quality as well as lifetime performance.”
Virtual Prototyping in the Heavy Industry is Trusted By
All over the world, suppliers, manufacturers, and engineering partners use ESI’s solutions to design and optimize heavy machinery, such as ABB, AP&T, Arcelor Mittal, Bosch Rexroth, Caterpillar, CNH, Epiroc, Fuji Electrik, Gabler, Hitachi, John Deere, Jungheinrich, Komatsu, Liebherr, Lenze Drives, Mitsubishi Electric, Palfinger, Putzmeister, Romonta, Siemens Minerals, Siemens Large Drives, Tenova Takraf, United Technologies, and Voith Paper.