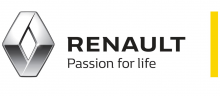
Renault Improves Yield and Produces Over 520 More Parts per Hour
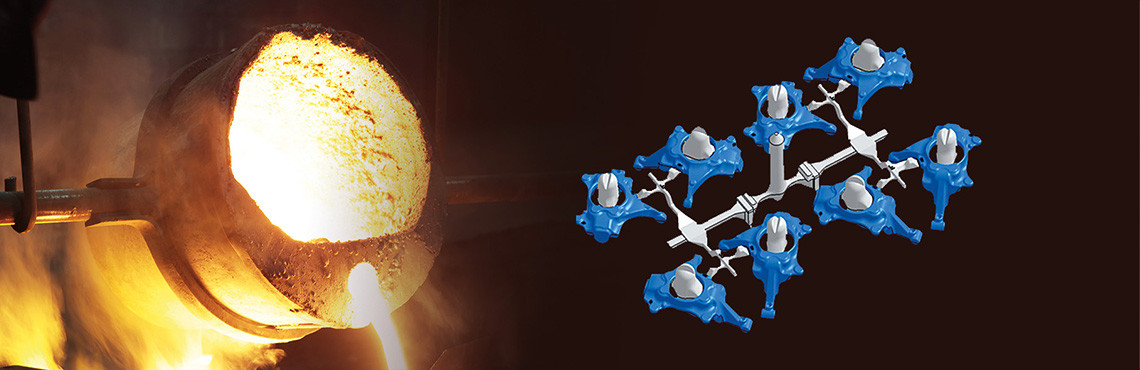
After using ESI QuikCAST, not only were we able to increase our bottom line by saving on metal and creating more castings than before, but we also implemented a completely new system for casting that we now use routinely across various product lines within the company.
Laurent SOULATCasting Specialist / Renault Process Engineering
Story
Fonderie de Bretagne (FDB) joined the Renault Group in 2009 and is now a wholly owned subsidiary. The company produces rough and machined parts in spheroidal graphite cast iron and other materials. Renault has made a considerable investment in installing a new molding line at FDB. In the scope of commissioning the new line, Renault decided to standardize their production methodologies and to use simulation early in the development cycle. This meant devising a standard for creating molding layout and feeding design that could be replicated across a wide range of casting products. For the pilot project, they chose an existing 6-cavity mold layout of a cast iron knuckle; one already in production but experiencing some noticeable shrinkage porosity problems.
They started from scratch as they would with any new product. First, using the ESI QuikCAST simulation software, they performed a single casting simulation with no filling or feeding system, simply observing the solidification in the sand mold, with a starting temperature close to the pouring temperature. The natural thermal gradients of the casting were used to identify the solidification path and pinpoint the last solidifying regions in the casting.
Next, they created various practical feeding designs and performed a complete simulation of each proposed design to identify the one leading to the best solidification pattern and without signs of shrinkage porosity in the casting. Having identified a suitable feeder, a similar exercise was repeated with multiple gating options in order to identify the optimal in-gate position and size; one offering the best filling behavior and solidification pattern.

The final, and arguably most important, step was to expand this optimized single-cavity design into a multiple-cavity mold. Renault improved the knuckle mold from a 6-cavity 97kg to an 8-cavity 82kg cluster. The new design solved the shrinkage problem, which had plagued earlier production, and provided a remarkable yield improvement; saving 37% in metal for every part produced. Furthermore, the new design produced two additional parts per mold, delivering over 520 additional parts per hour. The cost savings with the new design was substantial, to say the least.
Ultimately, thanks to the use of ESI QuikCAST, Renault resumed production of the Spheroidal Graphite Iron “Renault Traffic Front Knuckle”, and illustrated the standardized methodology built during the commissioning of its new molding line at Fonderie de Bretagne. Renault now uses this methodology successfully across different product families within the company.
About Renault
Our group, which has been making cars since 1898, is present in 134 countries and has sold 3.8 million vehicles in 2019. To meet the major technological challenges of the future while continuing to pursue our profitable growth strategy, we are focusing on international expansion and drawing on the synergies of our five brands: Renault, Dacia, Renault Samsung Motors, Alpine and LADA.
For more information visit Renault
Story release date: June 25, 2018