SimulationX
Multi-domain System Simulation Software
Modern mobility & machinery products are complex, connected, and dynamic systems. They consist of a multitude of components and subsystems, usually based on diverse technical domains, and are increasingly fitted with sensors and controls. Their dynamic interactions have a significant impact on safety, performance, and comfort.
With ESI's SimulationX software, engineers model, simulate, and analyze the behavior of all parts of the technical systems comprising mechanical, hydraulics, pneumatics, electronics, thermal, and control systems. Comprehensive component libraries with application-oriented model elements ensure that they have the right tools available for each task.
Discover Vehicle Systems Discover Fluid Power Systems Discover Energy Systems

SimulationX User Conference 2024: Watch Recordings Now!
Dive into digital innovation and system simulation technology with industry experts at the SimulationX User Conference 2024. This hybrid event features keynote talks, success-driven user presentations, networking opportunities, and exclusive updates from the SimulationX team.
Event Highlights at a Glance
- Keynote Talks: Explore transformative digital solutions.
- User Presentations: Learn from industry success stories.
- Exclusive Updates: Insights from the SimulationX core team.
For more details on abstract submission and participation, visit the event page:
What is the Value of the Full System Simulation Software SimulationX?
Robustness & Transparency
- Improve the robustness and reliability of your products by extending test coverage through virtual testing.
- Make design problems transparent by foreseeing unexpected effects and malfunctions very early.
- Validate, optimize & access system performance as you move along the timeline.
- Rich user experience with powerful tools, comprehensive libraries, easily accessible interface, extensive e-learning, and direct support.
Costs & Time Saving
- Shorten development time by using virtual models to quickly test the effects of various design changes.
- Save design and iteration costs by front-loading design changes and validation of their impact and maximize the ROI.
- Reduce physical prototyping efforts and thus related cost and time.
- Carry out extensive simulation-based experiments to identify potential design problems early, when the cost to change is small.
List of Engineering Libraries Available in SimulationX!
Access a broad range of specific libraries and simulation models - all on one platform.
"Over the next 10 years, industries must advance to larger, more complex systems. Tools like SimulationX allow us to model these vast systems."
Francisco ChinestaScientific Director, ESI Group
What are the Software Features that System Simulation and Modeling Engineers Appreciate Most?
These are the main SimulationX software features that empower customers to shorten development cycles and front-load decisions on design changes by visualizing the state and performance of the whole system or parts of it:
Develop Next Generation Mobility Types With Full Virtual Vehicle Modeling and Simulation
Virtual prototyping and virtual testing are crucial in today's mobility industry because of their ability to meet increasing market demands and ensure products adhere to industry requirements and quality standards. When integrated into the design and engineering process, these tools enable customers to deliver innovative and scalable products. SimulationX leverages the power of 1D modeling, allowing for early design changes and validation. This approach ensures that results are transparent and accessible at any point in the development process.
By modeling and testing subsystems and other parts of the system like propulsion systems, energy, HVAC, electronics, and sensor systems as a whole, SimulationX facilitates comprehensive vehicle development.

Improve Control, Precision & Effectiveness of Fluid Power Systems
The complexity of fluid power systems is inevitable due to the involvement of fluid, mechanical, electrical, thermal & control systems all together. Depending on the application and industry, hydraulic or pneumatic systems are used to deliver high precision, faster response time, and high power density. In today’s mobility and machinery industries, fluid power systems play an important role in building versatile, durable, and reliable products.
With a legacy of modeling hydraulics & pneumatics systems accurately for years, SimulationX has a wide area of applications covered, spanning various industries. Modeling mechatronic systems in heavy machinery with hydraulic actuators and control units is one of the strong areas of SimulationX.
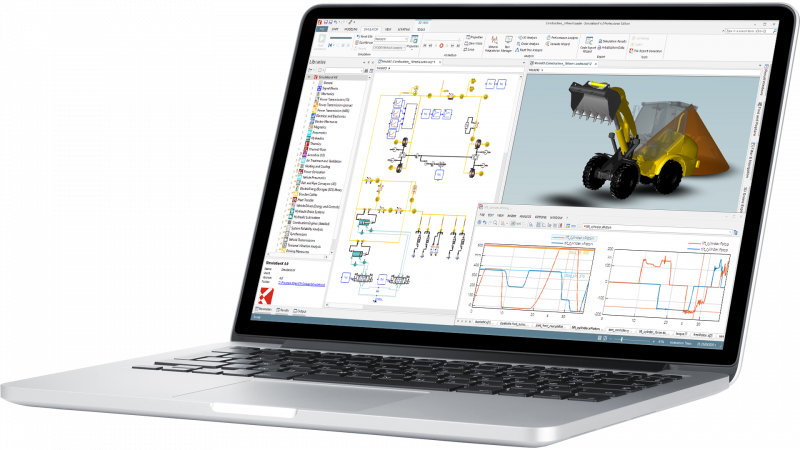
Identify, what is the best System-level Strategy for Effective Electrification & Energy Management
Complex requirements concerning energy efficiency, renewable energies, and electrification demand a solution approach that is safe, sustainable, and cost-effective. Especially automotive electrification technology is an emerging global trend. Producing, storage & distribution of energy using alternative energy sources like solar or hydrogen is gaining recognition in energy grids, the commercial and industrial space, as well as in heavy-duty transportation.
SimulationX delivers tailored solutions for EV battery range prediction, energy management, green hydrogen & alternate energy sources with its comprehensive library support and continuous development towards newer and innovative energy solutions.
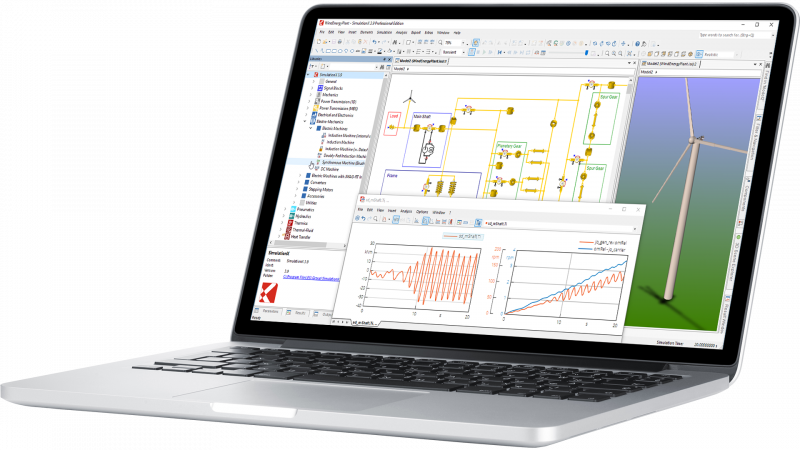