To push the boundaries of aircraft performance, aerospace companies must carefully balance cost, quality, safety, functionality, and resource use. Achieving energy efficiency, safety, and lightweight design goals requires early evaluation of material choices, geometries, production costs, and logistics.
With traditional manufacturing reaching its limits, new materials and processes are essential for extending flight range and reducing carbon emissions while maintaining safety. However, future designs must be assessed for manufacturing feasibility from the start.
Virtual Manufacturing is addressing this challenge by allowing engineers to simulate and validate manufacturing processes early in the development cycle. This ensures that proposed designs are practical and contributes to minimizing risks, optimizing efficiency, and accelerating innovation.
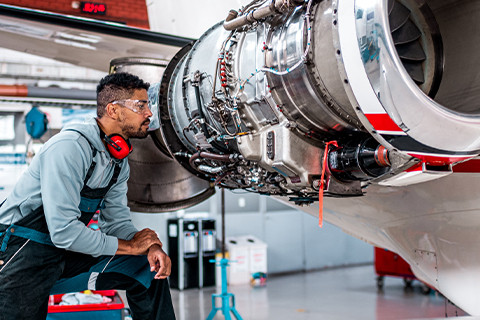
The Advantages of Virtual Manufacturing for Aerospace Components
Reason #1
Shorten Lead Times
Engineer a robust process delivering required part quality from first try-out
Reason #2
Detect Product & Process Anomalies Early
Identify and resolve defects before they impact production
Reason #3
Frontload Decision Making
Make smarter choices early to avoid costly delays and late part modifications
Reason #4
Minimize Physical Prototypes
Reduce reliance on prototypes with accurate virtual testing
Reason #5
Validate Feasibility & Safety
Ensure designs meet safety and performance standards upfront, considering as-manufactured conditions
Reason #6
Seamless Collaboration
Enhance teamwork with shared insights and shorten feedback loops during design iterations
Are you ready to take your aerospace manufacturing processes to the next level?
Watch our webinar to learn how Virtual Manufacturing can improve margin and overall product quality while reducing material and manufacturing costs and shortening lead times…
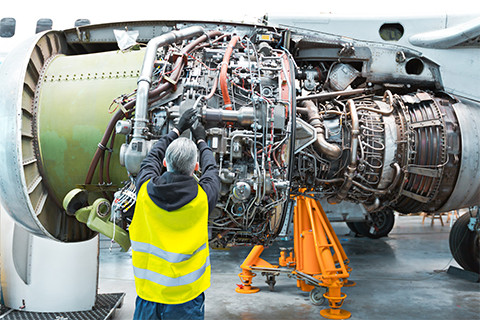
Utilizing the ESI Virtual Manufacturing Portfolio
Foster collaboration and alignment throughout your entire product development and production phase — engineer with confidence sheet metal forming processes, sand casting, investment casting, and resin-infused or pre-preg composite components.
Download our new eBook and get further insights into the challenges facing the Aerospace industry.
Learn more about how adopting a Virtual Manufacturing approach with the use of simulation software is helping to solve them.
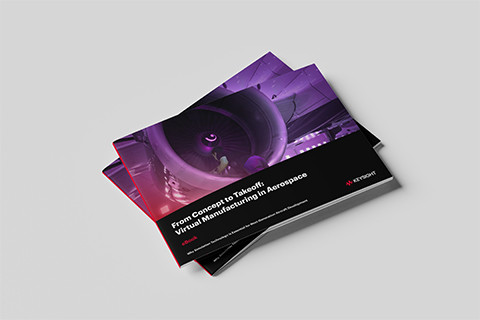
Check Out Some of Our Additional Resources to Learn More
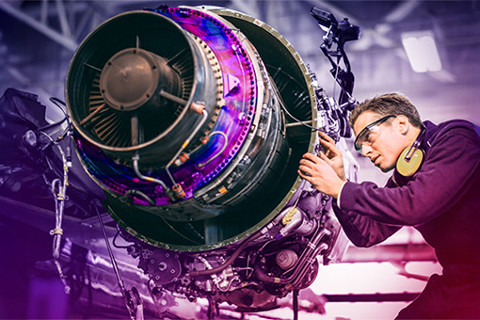
Blog: Mastering Advanced Casting Techniques for Modern Aerospace Manufacturing
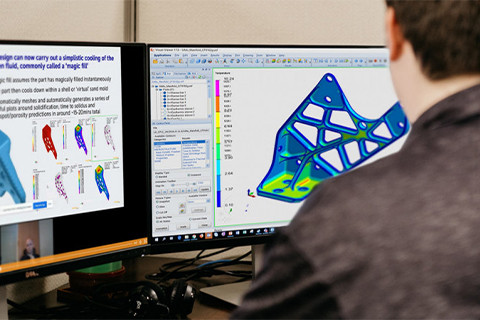
Customer Story: Co-design at Rolls-Royce, a “smart customer” approach to work with the supply chain for cast parts
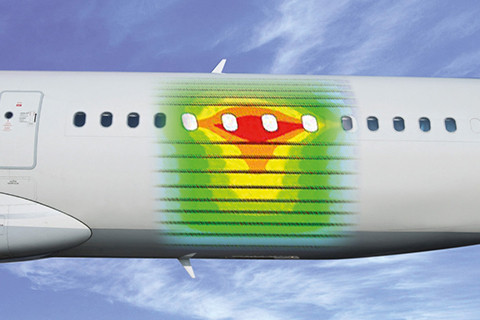
Blog: Composite Materials in Aerospace Manufacturing: Finding the Balance between Strength, Weight, and Safety