VA ONE
Simulation and Analysis Software for Space Structural Dynamics
ESI’s advanced vibroacoustic analysis software VA One is the de-facto standard for Space Structural Qualification, entrusted by NASA, the European Space Agency, and many space leaders including Boeing, Raytheon, and Northrop Grumman.
It is used by space engineering departments globally as a complement to physical testing to ensure space structures will survive launch, liftoff, ascent, separation, and re-entry stages. Space engineers also use VA One for meeting goals for operator comfort and safety.
VA One provides an all-in-one solution for simulating low- to high-frequency challenges, providing capabilities for Finite Element Modeling (FEM), Boundary Element Modeling (BEM), and Statistical Energy Analysis (SEA). Specific modules including Ray Tracing and DFAT® modules will assist you in achieving certification goals.
"VA One is intuitive and straightforward to use. I was able to complete a detailed coupled Boundary Element analysis the first time that I used the code”
Jeffrey LarkoAerospace Engineer Structural Dynamics, NASA GLENN Research Center
De-facto standard engineering software for testing the structural integrity and achieving the acoustic qualification of space hardware
VA One empowers space engineering teams to run accurate vibro-acoustic analysis and design across the full spectrum. Here are a few applications for which VA One provides the best answers possible:
Assess the strength of acoustically sensitive structures and frames to ensure mission success
The environmental loads experienced during launch, flight, and deployment can easily damage the space structures. And with the introduction of new, lightweight materials such as composites and honeycomb panels, the risk is even higher.
Space engineers only have one shot, therefore rigorous assessment is essential to gain confidence in the structural integrity of space hardware and reach acoustic qualification.
Space engineers trust the structural design and engineering software VA One to:
- Evaluate Mission Threats and safeguard structural integrity during the launch
- Determine the Sound Pressure Level (SPL) that your payload will have to sustain (SEA/Hybrid/FE)
- Validate dynamic stresses and forces of lightweight structures that can be easily damaged by acoustic excitation experienced during deployment
- Test hardware response to environmental loads experienced during launch, flight, and deployment across the full-frequency spectrum
- Establish pre-flight comparisons to assess optimal structural configuration
Use Ray Tracing to simulate stress and acoustic loads on the fairing, and to model liftoff environments for operator safety
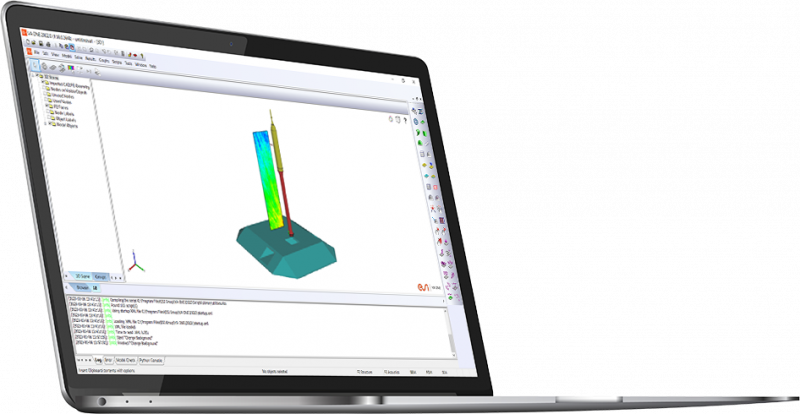
During liftoff, the exhaust plume generates a considerable amount of noise that induces high vibroacoustic loading conditions, which are complex and difficult to characterize.
VA One’s Ray Tracing module complements the existing FEM, BEM, and SEA capabilities of VA One so that space engineers can investigate the specific requirements:
- Perform accurate full frequency analysis
- Analyze large models at higher frequencies without incurring the large computational overhead
- Easily predict noise around the launch pad area
Diffuse Acoustic Field Simulation: Assess vibration levels on crucial components before they enter the reverberant rooms
Testing spaceflight hardware using reverberant chambers is standard in the space industry. Yet, the procedure remains extremely costly, depends on the availability of test facilities, and the need for transportation involves a risk to damage the test specimen. Aside from this, some tests may simply not be successful in delivering the information engineers need. Therefore, preparing for physical testing with VA One is a best practice for efficiently controlling the cost options in your testing budget, and accelerating product qualification.
Space engineers appreciate most the ease of use of ESI's comprehensive acoustic testing solution when:
- simulating different modal stresses, strains, and forces affecting crucial components
- Ensuring designs meet targets
- Optimizing weight
- Comparing alternative noise control strategies
- Assessing the structural integrity of delicate components
- Pre-qualifying designs prior to test
- Reducing the cost of testing
- Avoiding moving sensitive hardware to remote facilities for testing
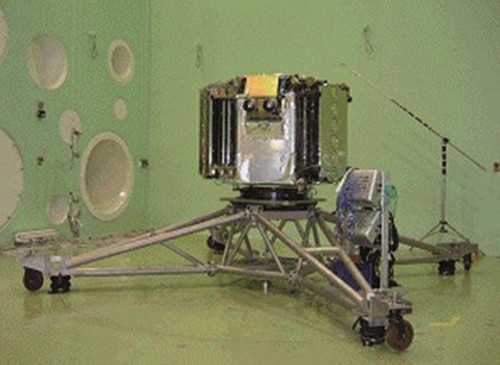
Courtesy of EADS
Set up for Success: Apply Structural Analysis Software to Prepare for Your on-site DFAT® Test
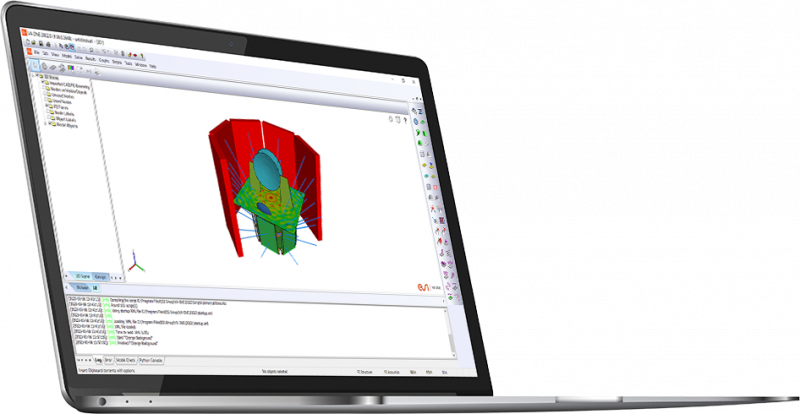
Acoustic testing of space structures requires the use of specialized acoustic reverberation rooms with high costs and availability issues along with the need to transport delicate instruments to testing facilities. New techniques for Direct Field Acoustic Testing® using flexible, powerful portable speaker arrays allows structural qualification testing to be performed on-site.
Space engineers use VA One to prepare for DFAT® tests and:
- Emulate a uniform diffuse acoustic field around the specimen
- Test various speaker configurations
- Deliver pre-test structural qualification
Use Structural Analysis Software to Simulate the Aero-Vibroacoustic Effects (AVA) Experienced During Liftoff
Space structures experience strong pressure as they travel through the atmosphere. Again, this can occur damage to the spacecraft and its components. Space engineers may simulate these phenomena by coupling VA One with a Computational Fluid Dynamics (CFD) code to
- Simulate Fluctuating Surface Pressure (FSP) by applying surface pressure excitation to FE structural subsystems, BEM fluids, or Fit Turbulent Boundary Layer (TBL) parameters from surface pressure
- Characterize Wavenumber-Frequency Spectrum (WFS)
- Apply GSP (General Surface Pressure)
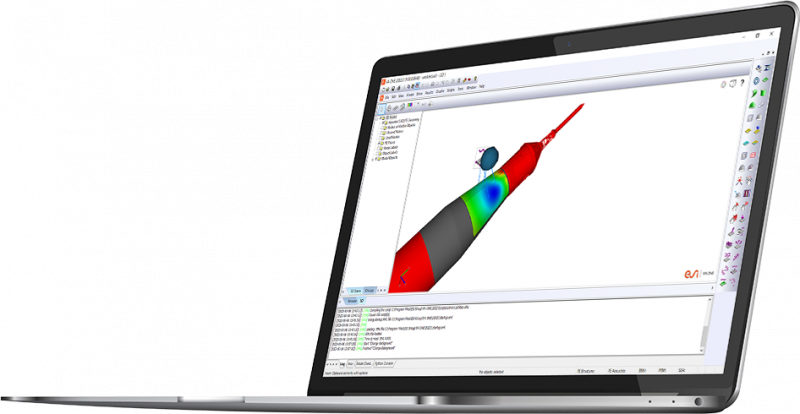
Predict High-frequency Shock to Safeguard the Integrity of Your Components by Leveraging ESI's Structural Analysis Software
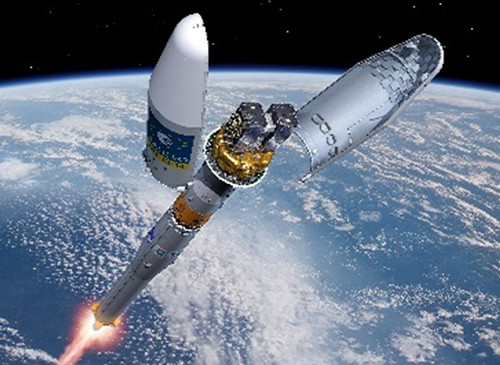
- The high-frequency shock induced by the separation stage of a rocket or space hardware can damage electronic components, create cracked welds, short-circuit/dislodge connectors, or fracture component mounting bolts.
- Damage can be subtle, not always repeatable, and not always exposed in a one-time test, which is why Virtual Modal Synthesis and Simulation (VMSS) is a must.
- VA One’s SEA capabilities can be used in conjunction with its Shock Module and ESI or third-party Impact Dynamics codes to support space engineers in precise shock prediction, for testing interconnected plates, missile interception, and many other applications.
"The VA One Shock Analysis tool enabled Boeing and NASA to assess potential damage to Space Station electronic boxes that might occur from inadvertent impacts during on-orbit assembly. The VA One Shock Module ensured that the current assembly operations would not affect critical Space Station hardware and eliminated the need to implement expensive operational and hardware changes."
Ed O’KeefeAssociate Technical Fellow in Noise and Vibration - Boeing