Discover how ESI's Virtual Prototyping Tools Realize Best-in-Class Processes and Profits
By immersively visualizing future products and components, analyzing product integration, and synthesizing human-centric assembly and maintenance processes, aerospace and defense manufacturers can avoid costly and limited physical prototype testing without compromising accuracy, safety, or time-to-market.
Discover how our innovative aerospace digital solutions can transform your processes and profits - watch our video to find out more.
During the last decade, aircraft manufacturers have been in a race for mass production, often delaying the adoption of smart digital technologies. Then, the pandemic has forced them to take a step back, allowing time to prepare for the necessary structural transformations and to expand digital capabilities in order to prepare manufacturing operations for the re-start. Nowadays, shifting away from traditional development methodes towards applying more virtual prototypes. aircraft manufacturers gain more agility to launch new programs faster than ever before, to reach greater levels of industrial efficiency, and to establish greener and leaner processes – less scrap and power consumption, more throughput, more profitability.
Investing into 4.0 technologies to extend existing digital capabilities may look like an extra financial stretch at first glance, yet, this is mission-critical to anticipate business recovery, for both manufacturers and suppliers. Stand-alone CAD and CAE designs using empirical and historical safety margins and traditional test-and-learn protocols relying on physical testing will be abandoned for an end-to-end digital thread that seamlessly connects product design, manufacturing, and in-service operations across. This is what we, at ESI, call Virtual Prototyping.
Virtual Prototypes empower engineers to digitally validate a design’s performance in terms of product quality, production capacity utilization, safety, and security, or in terms of operations and maintenance costs. It brings confidence about manufacturability and the most efficient manufacturing process in the early development stages. Supplemented with Hybrid Twin technologies, engineers are equipped with the ability to experiment virtually with real data and real physics, simultaneously. This is the extra degree of freedom and early confidence engineers need to design, manufacture, and assemble right the first time - without real tests or prototypes, before cutting a single piece of metal, and with zero downtime during final operations.
What is Exactly Meant by Virtual Prototypes? Let's See Some Examples Showing Their Use And Benefits for Aerospace And Defense.
Driven by operational challenges such as overcoming barriers to innovation adoption, meeting sustainability KPIs without compromising on additional business priorities, and ramping up digital transformation, aviation manufacturers are exploring new ways to reach greater levels of industrial efficiency.
Want to learn more? Download the whitepaper and discover how virtual prototyping could help you safely and sustainably achieve flight and air mobility breakthroughs.

Get Acoustic Qualification Right First Time
Test and certify new air and spacecraft designs with your very own virtual acoustic chamber: get noise certification right the first time to ensure superior sound quality. The fully virtual, emission-friendly test system can identify discrepancies early on, and test and certify vibroacoustic performance whilst minimizing processes, tooling, and scrap material costs.
Ensure Superior Sound Quality
Achieve desired comfort levels with reduced interior and exterior noise emission and create a quiet comfortable in-cabin air travel experience for passengers.
Read more about ESI Acoustic Performance Simulation Solutions
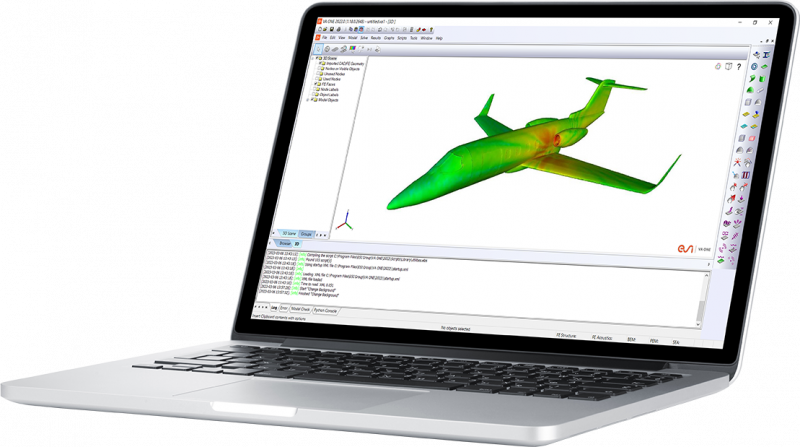
Speed up Space Structural Qualification
Virtually qualify space structural dynamics safely, fast, and at a low cost, minimizing the need for expensive remote test facilities.
Read more about ESI Acoustic Performance Simulation Solutions
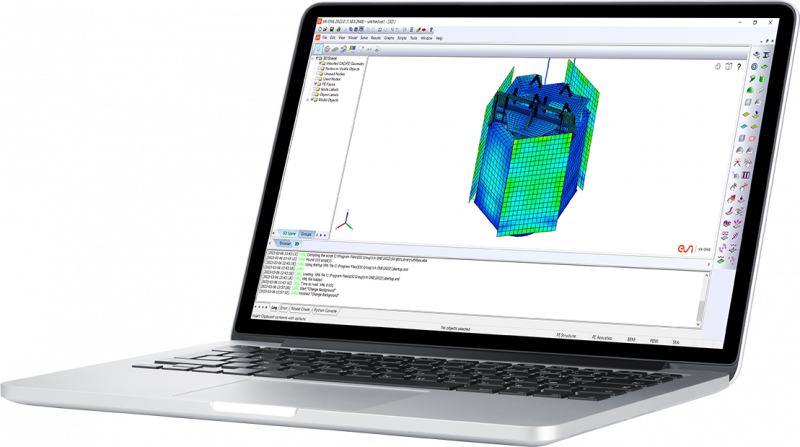
Create Quiet eVTOL Aircrafts with Virtual Prototype Tools
eVTOL is a modern-day innovative aircraft that uses electrically powered systems to hover, take off, and land vertically. System-based verification methods are useful to analyze the drivetrain sizing, flight controls, flight dynamics and battery sizing, safety & cooling. Further Vibro-Acoustic solutions help to analyze the exterior noise impact in urban areas as well as interior noise level comfort. Discover how ESI solutions allow virtual design iterations on the eVTOL performance and safety, and meet noise regulations.
Power Collaborative Virtual Workflows with 3D Immersive Prototypes in the Industrial Metaverse
Push engineering workflows months ahead of production by creating your own industrial metaverse. Experience physical interactions with yet-to-be-realized aircraft designs without waiting for the construction of physical prototypes and collaborate with colleagues without having to travel to a common site. Immersively explore new aircraft concepts from a worker and operator perspective and gain hands-on experience of the processes required to make and maintain them.

Human-Centric Process Validation and Product Integration
Use Virtual or extended Reality to build interactive immersive experiences that validate human-performed process validation and complex product integration.
Find out more about our Virtual Reality Solutions for Aerospace and Defense
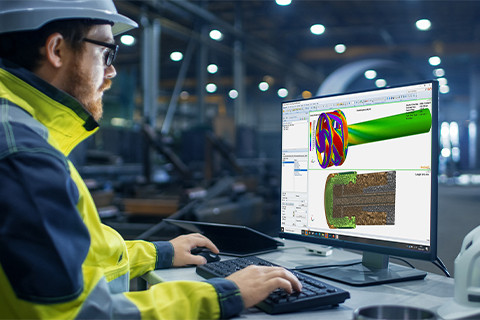
Virtual Manufacturing of High-Precision Parts
Achieve the highest material performance by using simulation-based testing. Gain a deeper understanding of material physics with unlimited analyses and experiences, which is impossible to do with physical tests and trial & error. Create stable, robust manufacturing processes to secure production ramp-up, minimize scrap costs, save natural resources, and ensure on-time delivery.
Virtual Prototyping in Aeronautics is Trusted By
All over the world, suppliers, manufacturers, and engineering partners use ESI’s Virtual Prototyping Solutions to design and optimize future mobility in the air, e.g. Airbus, Alcoa, Avic, Boeing, Bombardier, Dassault Aviation, ESA, General Dynamics, Joby Aviation, Honeywell, Lockheed Martin, MSI-DFAT, MTU, NASA, Northrop Grumman, PCC, Rolls Royce, Safran, Textron Aviation, Thales, United Technologies and many more.