Multi-Material Assemblies in Body Chassis Manufacturing
Multi-material assemblies are key to producing vehicle bodies with the most efficient cost/lightweight ratio. However, it is a challenge to find the right material mix and apply it to the appropriate location, optimize geometries & thicknesses, engineer robust manufacturing processes, and select the optimal joining technologies. Due to an almost infinite number of combinations, single-point numerical simulations aren’t enough to get the job done.
Instead, automakers have started to shift towards tightly coupling the engineering and manufacturing worlds to make the right decisions as early as possible in the development cycle and avoid late correction loops with costly physical prototypes.
For most steel-based body structures, end-to-end virtual prototyping is an established approach for OEMs – from connecting the product design, performance, and manufacturing engineering workflows. Some key benefits are:
- Confidence in the best design earlier by predicting manufacturing, assembly and performance through accurate representation of physics and applied processes
- Accurate manufacturing and performance validation of all lightweight materials (standard steel, high-strength steels, aluminum, composites) regardless of what process they have been manufactured through (standard stamping, hotforming, casting)
- Unlimited virtual try-out to find the most efficient manufacturing processes to achieve assemblies with optimal cost/quality ratio ensuring correct performance
- Reduction (and eventually complete elimination) of expensive physical prototypes and time-consuming try-out iterations
Ultimately, end-to-end virtual prototyping is the best way to reduce your overall product development cycle, cost, and time to the start of production (SOP) by getting your sustainable vehicle engineering, manufacturing, and assembly processes right.
Discover the transformative power of ESI's virtual prototyping solutions in revolutionizing car body and chassis manufacturing. This video explores solutions that pave the way for transition from physical to virtual testing, significantly reducing development time and costs, while enhancing vehicle safety and performance.
Watch Mark Vrolijk as he introduces:
- PAM-Stamp: to simulate sheet metal forming and predict issues like cracks in lightweight designs.
- ProCAST: and how to analyze casting processes for quality control.
- PAM-Composites: to model composite materials for strength and lightness.
- SYSWeld: to simulate welding processes to predict quality and distortions.
This video also addresses the challenges of handling high-strength steel, aluminum components, and complex castings before discussing the merits of 'virtual value chains' that connect manufacturing, assembly, and performance for optimal final assembly quality, improved safety, and accelerated time to market.
How Multi-Material Assembly Simulation Supports You Throughout the Entire Vehicle Development Cycle
Being able to introduce manufacturing information early in the virtual prototyping chain is beneficial for all stages in the product development cycle.
- Product design | Delivering reliable feasibility analysis and material cost information quickly when iterating on parts made of challenging materials
- Performance engineering | Enabling early crash and durability/ NVH performance analysis on ‘as manufactured’ (sub-) assemblies, by including the forming and assembly/joining history
- Manufacturing engineering | Efficient support for finding the optimal process route for delivering flawless parts, (steel, aluminum, composites) within tolerances and with expected quality
- Assembly engineering | Start to build assembly processes on realistic component geometries, including the distortions caused by the manufacturing processes and guarantee a final body or chassis assembly within tolerances
Design, Manufacture, and Assemble Mixed-Material Assemblies with Virtual Manufacturing Simulations
Let’s Get Manufacturing and Assembling Issues Right Together
For years, ESI has been working with OEMs and suppliers to create an end-to-end digital thread that ties together all the different stakeholders and activities in design, engineering, manufacturing, series production and maintenance. We accompany our customers in shifting their processes from single-point, purely numerical simulations towards end-to-end virtual prototyping – making sure they get single part design, manufacturing and assembling processes right the first time. This is the foundation to move forward with designing and manufacturing multi-material solutions for sustainable mobility devices.
What are the benefits from shifting from single-point numerical simulation to an end-to-end connected virtual prototyping workflow
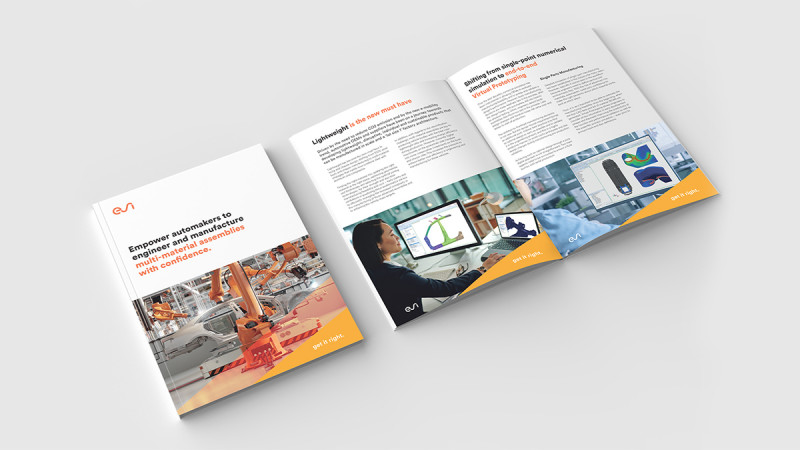
In a nutshell: Quickly develop confidence in new materials and manufacturing technologies. It’s all about predicting manufacturing processes at the engineering level and achieving an optimum design earlier and faster while minimizing the need for physical prototypes. This is key to getting our daily engineering and manufacturing practices more sustainable.
Download the whitepaper - Mixed-Material Joining Simulation - to learn more about how OEM workflows are shifting from single-point numerical material and process simulation to end-to-end connected virtual prototyping workflows.
Virtual Modeling for Mega Casting
Mega Casting, also known as Giga Casting or Hyper Casting, is a game-changing method for creating large aluminum car parts. It promises a future where cars are lighter and more efficient. But with big innovations come big risks. By simulating every part of the Mega Casting process, you can spot and fix potential problems before spending a lot on tools. This helps optimize designs and ensure smooth production, making the future of car manufacturing much more seamless.
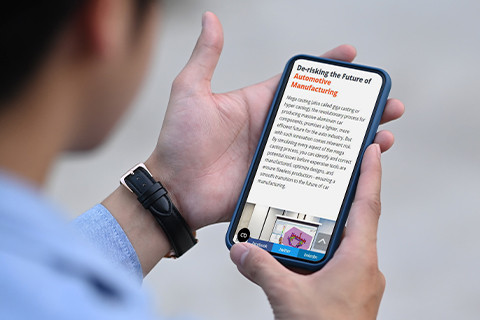
We invite you to walk this path together and engage with us. Challenge our expertise and knowledge in the physics of materials and predictive numerical simulation.
Are you ready?