VA ONE
Software for Vibro-Acoustics Analysis & Simulation
Accurate predictions to ensure designs meet legislative specifications for issues such as pass-by, underwater, and cabin noise must be early in the design phase for most industries. Particularly for the automotive industry, interior noise is a crucial product selection differentiator for the end-users. The current industry practice of relying on late-stage test procedures to identify vibro-acoustic performance can negatively impact both product cost and performance.
ESI VA One is a single environment for aero-vibro-acoustics analysis and design. It allows engineers to perform accurate predictive noise and vibration design assessments early in the design cycle to meet product performance objectives. Users can meet aggressive design-time constraints, ensuring engineering decisions can be made when they most benefit the demands of a multi-disciplinary development environment.
The VA One environment is accessed from a standard user interface, covering all frequency domains through a set of seamlessly coupled and proven modeling methods. With VA One, users achieve optimal design productivity without the need to deploy separate solutions requiring training for different user interfaces and data exchange between environments.
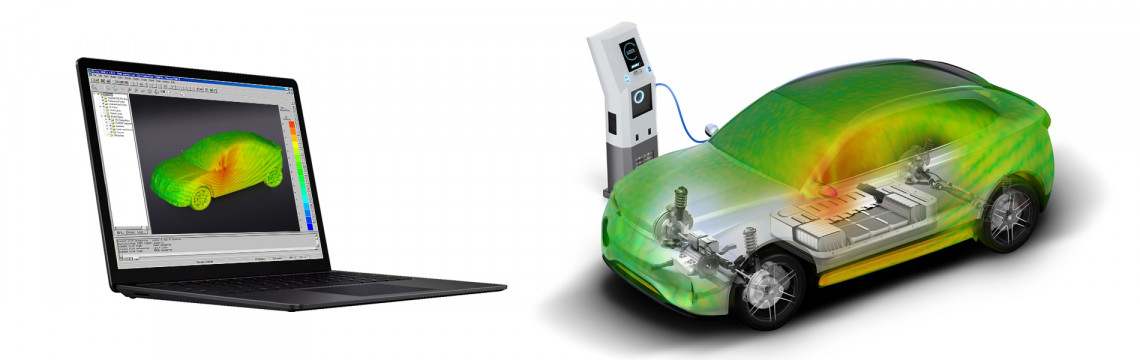
Benefits of VA One for the Vibro-Acoustic Analysis of Complex Systems
- Meet operating targets (quality, cost) and achieve project milestones with accurate noise prediction models early in the design process
- Integrate noise prediction tools into existing design environments to quickly assess prototype designs with rapid model creation
- Access an optimal set of seamlessly coupled, fast methods to minimize simulation time
- Evaluate your design and rapidly test countermeasures to meet attribute targets
- Achieve design objectives for interior and exterior noise within a single environment
- Eliminate expensive, late-stage modifications
The project proved that ESI’s VA One is capable of accurately predicting the vibro acoustic performance of complex designs allowing design engineers to refine proposals before committing to expensive prototypes.
Renny RantakokkoM.Sc. Noise and Vibration Specialist / Epiroc Rock Drills AB
How Can Vibroacoustic Performance Simulation Transform Your Engineering Projects?
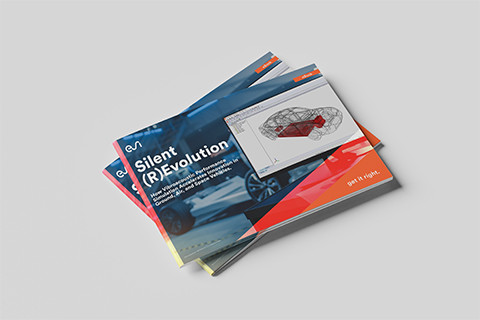
Discover the game-changing potential of advanced vibroacoustic simulation techniques with this comprehensive eBook: Silent (R)Evolution - How Vibroacoustic Performance Simulation Accelerates Innovation in Ground, Air, and Space Vehicles.
Inside, you will see how to...
- Unlock Innovation and Optimize Workflow.
- Reduce Costs and Improve Accuracy.
- Ensure Space Mission Success.
- Accelerate automotive design, testing, and development.
- Exceed Performance Expectations.
The Acoustic Boundary Element Module (BEM) contains all the functionality you need to model the low-frequency response of bounded and unbounded fluids within the VA One environment (can optionally include Fast Multipole Boundary Elements for solving large models). The Acoustic BEM simulation module is the evolution of the RAYON Boundary Element solver and enables you to create accurate models of fluid loading, scattering, radiation, and transmission of sound at low frequencies.
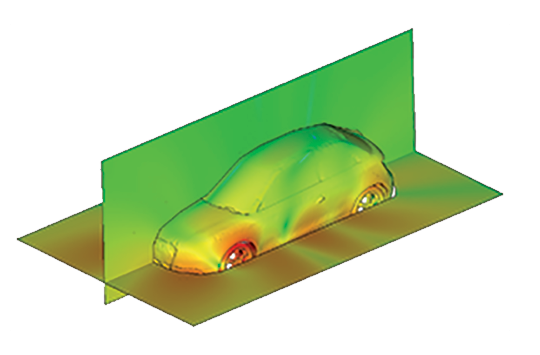
Features:
- Advanced Fast Multipole Boundary Elements for large models
- Indirect, Direct and Mixed Boundary Element methods
- Inbuilt mesh coarsening and “shrink wrapping” algorithms
- Automatic creation of fluid and data recovery meshes
- Full support for non-compatible structural and fluid meshes
- Full structural-acoustic coupling and random vibration analysis
- Complete library of acoustic loads: monopoles, plane waves, diffuse fields, etc.
- Infinite planes, rigid planes, pressure release planes, baffles
- Advanced Multi-Domain BEM
- Fully coupled solution (BEM fluids fully integrated within VA One)
Statistical Energy Analysis & Trim Modelling
The Statistical Energy Analysis (SEA) module of VA One is the evolution of the industry-standard software for mid and high-frequency noise and vibration design, AutoSEA2. The SEA simulation module is used routinely in virtually every industry for which sound and vibration are of concern. Find out why so many companies have made ESI’s software a standard part of their noise and vibration design process as well as in their statistical energy analysis.
Features:
- Full library of materials (isotropic, orthotropic, viscoelastic, foam/fiber, etc.)
- Full library of physical properties (uniform, ribbed, laminate, composite, etc.)
- Complete library of SEA subsystems (beams, plates, shells, cylinders, ducts, acoustic cavities, semi-infinite fluids, etc.) and structural and acoustic loads
- Account for pressurization, fluid loading, stiffening from curvature
- Automatic calculation of SEA coupling loss factors for point, line and area junctions based on full-wave transmission theory (and advanced radiation efficiency algorithms)
- Easy to use 3D modeling environment, visibility tree, and object-oriented database simplify model creation, model management and diagnosis of results
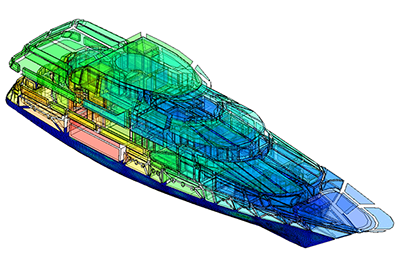
Wind noise is an essential aspect of vehicle performance. It impacts interior comfort and perceived product quality, which directly affects the passenger’s experience. The successful deployment of vibro-acoustic simulation and the resulting improvements to vehicle acoustics has led to reduced interior noise from sources such as powertrain, tires, and suspension. However, this results in a relatively more significant contribution from wind noise to the vehicle interior. Because wind noise directly influences the passenger’s ability to communicate with other occupants or make use of hands-free devices or phones, it is considered a vital product selection criterion. It is consistently ranked as a top concern for overall vehicle quality.
The growing speed and efficiency of Computational Fluid Dynamics(CFD) simulations result in greater accessibility to time-domain pressure distribution predictions. Turbulent flow can now be effectively simulated and processed to provide vibro-acoustic model excitations up to the higher frequencies that most strongly affect interior noise. The combination of CFD data and vibro-acoustic analysis as an ‘end-to-end’ solution for Aero-Vibro-Acoustic (AVA) simulation reduces dependence on expensive wind tunnels, whose availability is minimal. Allowing designers to virtually model interior acoustics excited by turbulent pressure fluctuations enables design decisions to be made earlier in the design cycle, reducing the need for costly revisions in later design stages.
ESI’s VA One Aero-Vibro-Acoustic module automatically converts CFD pressure-distribution time histories from a wide range of formats into the appropriate Fluctuating Surface Pressure load or input power in the frequency domain. Both types of dominant excitation components, convective and acoustic, are derived from this CFD pressure data and applied to structures and fluids in the vehicle model to predict interior noise and support wind noise reduction and optimization through virtual design studies.
Features:
- Fewer expensive post-prototype modifications needed due to accurate prediction of flow-induced noise earlier in the design phase
- Easy-to-use tools and intuitive user environment offer seamlessly coupled methods, minimizing model building time and training
- Faster ROI and shorter learning curve is available through support infrastructure
- Proven customer success based on previous consulting projects

Ensure Structural Integrity of Satellite and Space Hardware From Acoustic Loading
Using lightweight materials, including composite and honeycomb panels, can be challenging, especially when the end-product is subject to high-intensity stresses but must comply with stringent launch certification requirements. ESI VA One simulation software enables satellite and space hardware designers to confidently design and build their product using high-quality composite materials to meet the optimum performance of the spacecraft through launch, flight, and deployment.

Features:
- Validate dynamic stresses and forces of lightweight structures that can be easily damaged by acoustic excitation experienced during deployment
- Accurately predict structural response of space hardware during launch by using Virtual Acoustic Engineering and DFAT® simulation capabilities avoiding the risk of having to move sensitive hardware to remote facilities for testing
Effectively Manage Aircraft Noise
Interior aircraft noises arise from exterior sources transmitted through a variety of paths into the interior and are coupled with onboard noise sources such as HVAC, pumps, and generators. This has the potential to greatly reduce passenger comfort, an extremely high priority for any aircraft operator. Engineering simulation is essential in meeting acoustic requirements without hindering on-time certification and production targets.
From engine noise to turbulent boundary layer (TBL) and shock cell, ESI VA One allows engineers to effectively optimize all potential noise sources in commercial jet aircraft. Meet safety standards and brand objectives for aircraft acoustics, while at the same time minimizing weight and avoiding costly late-stage interventions.
Here is an overview of the benefits of our full frequency acoustic simulation solution for aeronautical applications at a glance:
Features:
- Ensure optimal cabin & cockpit acoustic comfort with:
- Statistical energy analysis (SEA) a computationally efficient method for high-frequency noise analysis
- Ray Tracing for accurate rapid analysis of noise transfer compared with traditional deterministic tools such as BEM
- Confirm PA systems (Speech Clarity) perform to safety expectations
- Performing virtual acoustic modelling to meet operator acoustics targets for cabin brands including insulation optimization, aerodynamic and vibration acoustics, composite modeling and simulation of fuselage wall transmission loss
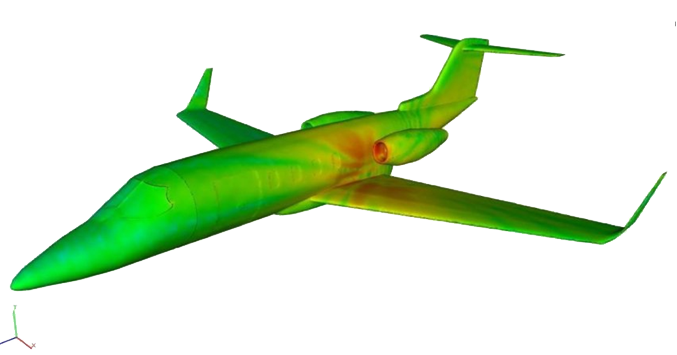
Fast Computation of System-Level Models for Interior & Exterior Noise Prediction
ESI VA One Ray Tracing offers a quick and accurate analysis of interior and exterior noise for any large or complex-shaped geometry such as a car, train, aircraft, spacecraft, ship or building.
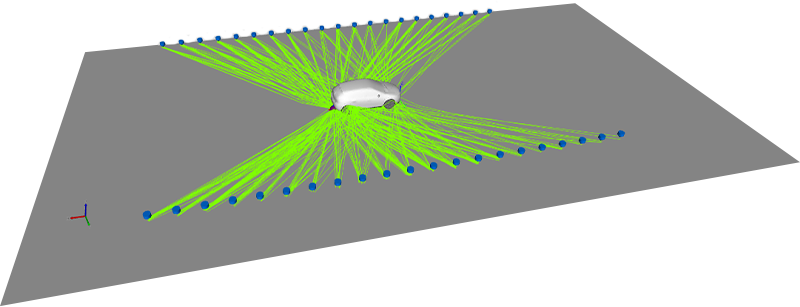
Features:
- Reuse VA One FE and SEA models to define the Ray Tracing geometry with no additional modeling effort
- Use Noise Control Treatments (NCTs), BEM complex impedances and absorptions from SEA and BEM models to evaluate and optimize trim effects
- Compact Acoustic Source (CAS) definition accounts for acoustic source directivity
- Run smooth and rough surface modelling using Snell and Lambertian laws
- Used for unique applications such as Speech Clarity and Pass-By Noise analysis
Accurately Model Acoustic and Vibration Response Across the Entire Frequency Spectrum
In the past, mid-frequency predictions, where both airborne and structure-borne transmission paths contribute to vibro-acoustic performance, required a choice of one of the following:
- Deterministic models using low-frequency modeling assumptions which become computationally expensive and less accurate at high frequencies
- Statistical methods whose accuracy and ability to predict point-to-point responses is often insufficient for structure-borne applications at low frequencies
The Hybrid Module is a state-of-the-art vibro-acoustic analysis method that allows users to perform a coupled calculation in the mid-frequency range, overcoming the challenges associated with the use of solely deterministic or statistical solutions in this critical region.
The ultimate in modeling flexibility, the Hybrid Module allows for the combined use of the best simulation methodologies to accurately model acoustic and vibration response across the entire frequency spectrum. Developed as part of a long-term research program by ESI in conjunction with leading academic institutions and industrial consortia, the Hybrid Module allows the user to create fully coupled FE/BEM/SEA models covering the entire frequency range within a single analysis.
Features:
- Create efficient system-level noise and vibration models across the entire frequency spectrum, including the challenging mid-frequency range
- Extend existing SEA models to mid and low frequencies by adding local FE subsystems to more accurately represent complex junctions and stiff components
- Refine model dominant transmission paths using FE subsystems and optimize junction designs to minimize structure-borne transmission and input power and optimize local constructions
- Extend existing FE/BEM models to higher frequencies and reduce computational expense, while capturing the physics of a problem, by using SEA to statistically model subsystems with high modal density
- Quickly add SEA acoustics, poro-elastic materials (PEM), and random acoustic loads to existing FE models. Perform Transmission Loss (TL), radiation efficiency and diffuse acoustic loading predictions in a fraction of the time it takes to perform a full FE or FE/BEM calculation
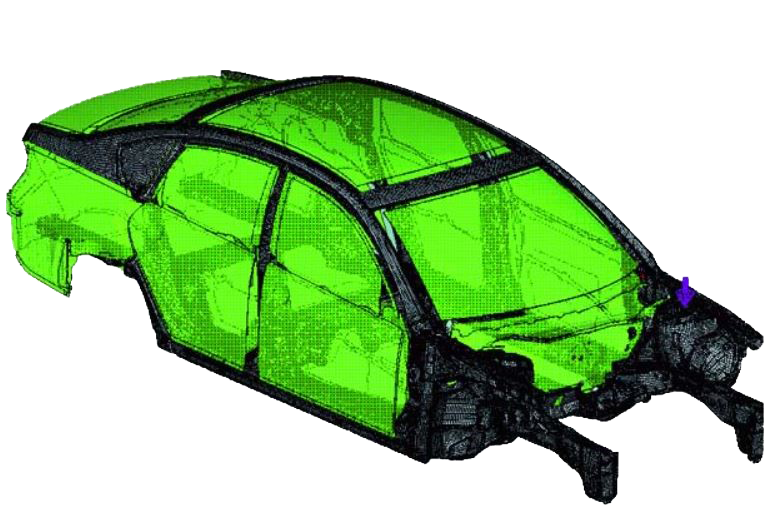
Low-Frequency Structural and Acoustics Response to Meet Design Goals
At low frequencies, vibro-acoustic response is strongly determined by receiver position details. Finite Element (FE) Analysis is used to simulate detailed structural or acoustics responses allowing designers to understand the dynamic behavior and develop countermeasures necessary to meet design goals. ESI offers solutions to support both acoustic and structural FE simulation as a standalone coupled or uncoupled solution as well as in conjunction with coupled FE/BEM models and Hybrid FE/SEA models.
The Acoustic FE Module gives you all the functionality you need to add fully coupled FE acoustic finite element cavity subsystems to your VA One models. This module is ideal for creating accurate FE models of enclosed acoustic cavities at low frequencies and for optimizing the low-frequency performance of poro-elastic material (PEM) noise control treatments.
The Structural FE Module allows the user to import existing models and results from a host of external FE solvers and to couple these results with FE/BEM calculations or other hybrid and advanced VA methods such as FE/SEA.
ESI offers the Vibro-Acoustics software user the same scalable and powerful Implicit FE solver used in the VPS NVH product. This high-performance solver with both structural and acoustic capabilities provides for maximum efficiency and seamless integration of FE calculations whether as standalone FE or coupled with the other VA solution methods.
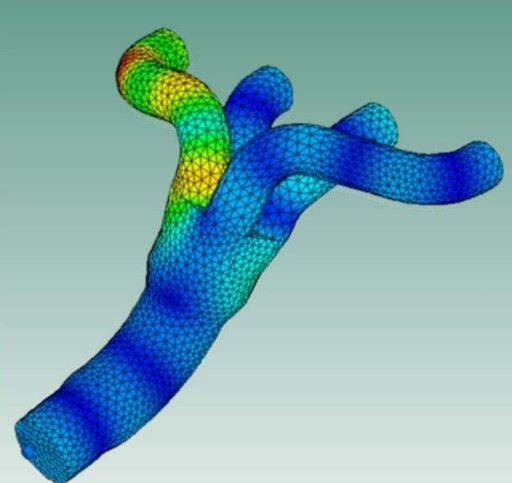
Features:
- Import external FE models and results for use with coupled or uncoupled FE/BEM calculations or hybrid or periodic FE/SEA calculations
- Create accurate vibro-acoustic FE models of acoustic cavities and structural components at lower frequencies
- Quickly and easily pinpoint the optimal location and lay-up of poro-elastic material (PEM) noise control treatments for maximum effective damping and absorption at mid and low frequencies
- Quickly perform a modal contribution analysis and gain insights into the parameters controlling the response at low frequencies