ESI to launch its Additive Manufacturing Simulation Solution at Formnext
Paris, France – November 6, 2018 – ESI Group, leading innovator in Virtual Prototyping software and services for manufacturing industries, will launch its Additive Manufacturing (AM) simulation solution on November 13-16 in Frankfurt, Germany at Formnext, one of the world’s largest tradeshows for next generation manufacturing technologies. Leveraging ESI’s unique knowledge of material physics and its long-lasting support of the world’s largest OEMs across industrial sectors, ESI Additive Manufacturing, provides a comprehensive solution to accelerate metal additive manufacturing developments. The solution’s ability to quickly address manufacturability issues on the shop floor, as well as connecting with material quality investigation, makes it the perfect solution to ensure efficient and continuous workflows from Computer-Aided Design (CAD) to parts qualification.
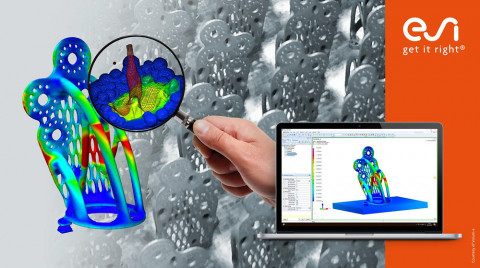
ESI Additive Manufacturing supports manufacturers of 3D printed metallic parts in achieving greater productivity, while providing key information on final parts quality. Photo courtesy of Volum-e.
Today, OEMs and their suppliers seize the opportunity to expand the capabilities of existing manufacturing processes by adding metal additive manufacturing. They seek to reduce assembly costs, to gain more geometrical freedom, to meet light-weighting goals, and to enhance mechanical performance. While doing so, they often meet the drawbacks associated with any new process adoption: long and expensive trial-and-error to secure parts design and validate processes. Not only must uncertainties linked to manufacturability be carefully investigated, but it is also essential to achieve precise levels of material performance, especially for part certification or qualification in regulated industries, such as aerospace. The risks associated with innovation must be mitigated to control development costs, and to provide a clear AM adoption strategy for industrial production.
Building on expertise in process simulation for metal manufacturing – including Welding, Casting and Sheet Metal Forming – proven over the past 2 decades, ESI delivers with ESI Additive Manufacturing a solution that overcomes today’s industrial challenges. ESI Additive Manufacturing addresses process engineering and manufacturing engineering departments, as well as 3D printing bureaus who seek rapid answers to essential questions including:
- Can my part be manufactured using Additive Manufacturing processes?
- What would be the best orientation / support strategy?
- What will be the impact on part integrity, including part distortion and residual stresses?
- Will I meet optimal material density and process throughput?
- What are the right parameters to prevent build failure?
Without building a hardware prototype, ESI Additive Manufacturing answers all these questions in a shortened time and with less associated costs. It provides a unique framework to achieve first-time-right prints. With ESI Additive Manufacturing integrated to ESI’s comprehensive platform of simulation solutions, future developments will deliver unique chaining capabilities to anticipate challenges linked to post-printing operations, including advanced heat treatment and machining.
Lionel Ridosz, Industrialization Development Manager at Zodiac Aerospace, working closely with ESI in the SOFIA project, sums up: “Detailed manufacturability evaluation is essential to find optimum adequacies between AM materials and processes, in a bid to increase the productivity of AM processes. Perhaps the most crucial aspect to see AM develop rapidly within the industrial landscape."
ESI Additive Manufacturing offers a unique solution to ensure continuous flow of information from concept, through manufacturing to certification. “To achieve manufacturing excellence in Additive Manufacturing, engineers must first understand and control the complex relationship between part design, 3D printing processes and material quality. This know-how is essential to engage in process qualification,” explains Dr Jean Sreng, Business Development Manager for ESI Additive Manufacturing. ESI’s Center of Excellence for Additive Manufacturing has been leveraging the company’s existing expertise in multiphysics, material science and integrated computational material engineering, to study the specific effects associated to Additive Manufacturing processes. Led by Dr Mustafa Megahed, ESI’s research teams are involved in numerous projects including DARPA Open Manufacturing, SOFIA and AMANDE. Working closely with industrial leaders including Honeywell, the team has published numerous technical papers on the challenging topics of AM material quality, process certification and qualification for aeronautics industries.
ESI and Honeywell will be sharing some insights on their collaboration at Formnext, on the TCT introducing stage on Friday, 16th November at 11:45 am in a presentation entitled: "Laser Powder Bed Fusion (LPBF) Right the First Time - The right mix between modeling and experiments."
For more ESI news, visit: www.esi-group.com/company/news