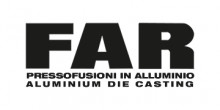
FAR Uses Simulation to Select the Right Die Casting Machine and Improves Production Rate and Margins

Today Casting simulation is mandatory and necessary to reach best quality results including choosing the right tonnage of the machine to reduce costs. Thanks to these results in quality and costs, FAR can be competitive in the market.
Gianfranco LenziCEO / FAR srl
Story
Since 1992, FAR has played an active role in the constantly evolving and challenging automotive sector, with dedication and innovation. FAR’s commitment to its clientele is to remain a reliable and proactive partner, leveraging the best technologies, offering their expertise in the die casting process, and ensuring close cooperation for better planning and problem-solving. Therefore, when a customer called on FAR to increase production on an automotive oil pump, it was only natural for FAR to seek out the most cutting-edge and effective approach.
FAR had been successfully producing this automotive oil pump on a single-cavity die using a Colosio 560 tons die casting machine (DCM). When their customer challenged them to increase production volumes, the obvious thought was to switch to a double cavity die. In doing so, however, they would need to keep costs low while, at the same time, maintaining the same high-quality castings. For that reason, choosing the best DCM was imperative.
The standard approach, using empirical evaluation, showed the necessity to use a 1000t-1200t DCM to produce this oil pump on two cavities – but the challenge for FAR’s technical & management teams were to manage with a smaller, more cost-effective 750t DCM. Also, to meet final quality requirements, FAR elected to use High Vacuum on the double cavity die, sharply decreasing air counterpressure during filling, to prevent gas porosity problems and reduce the injection force.
ESI collaborated with its partner ECOTRE Valente SRL to develop a new solution for FAR: a virtualized die casting machine integrated into the ESI ProCAST simulation software to account for the hydraulic injection force of the DCM controlling the piston movement during filling, as it would in real-time. The optimized piston speed profile could then be exported from simulation directly onto the DCM PLC system.
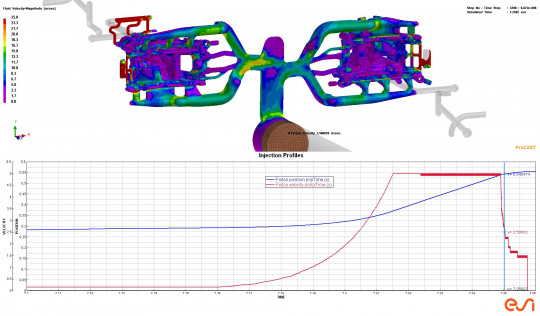
Ultimately, the simulation allowed FAR to optimize the gating and evacuation system of the double cavity die, making it suitable for the 750t machine. The vacuum system further reduced the required hydraulic injection force. With ProCAST, FAR identified the right DCM to produce a prospective cast part, ultimately reducing their parts cost by 28%. In addition to this, an estimated operational cost of 165k€ is saved per year, due to the virtual machine selection of Colosio 750 ton instead of Colosio 1200t machine.
About FAR
Our current and long-term goal is to be an always more reliable and proactive “high-tech” partner for our clients.
Our primary mission is to satisfy our clients in terms of products and service, offering our expertise in the die-casting process and ensuring a close cooperation aimed at better planning and problem-solving. In order to achieve our goal, our concept of business has changed over the years becoming the key element of our company, entailing moral and ethical obligations towards our stakeholders (employees, clients, suppliers…), towards the environment and, not least, the State. Every time we take a step forward, we are already focused on the next two.
For more information visit FAR
Story release date: February 19, 2020