Strengthening of ESI’s position in casting simulation among Spanish and Portuguese foundries
Dedicated to the foundry challenges, ESI’s Casting Simulation Suite, including ProCAST and QuikCAST, is a key solution to reduce manufacturing costs, shorten lead times for mold development and improve the casting yield and quality. The Iberian market has a high concentration of small to mid-size foundries supplying the industry worldwide. Recently, many of these Iberian foundries have decided to massively invest in simulation tools to optimize their processes.
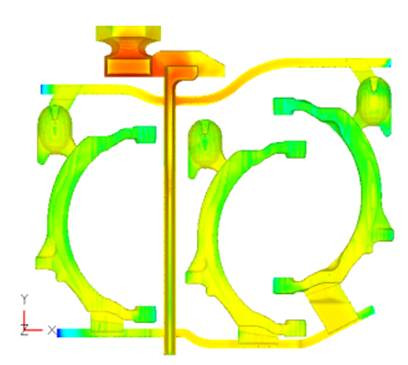
San Eloy Fundiciones
Following the success of the three Casting seminars held in Vitoria, Zaragoza and Madrid in April 2009, and organized by Análisis y Simulación, ESI‘s Casting agent in Spain, several sand foundries have chosen to invest in ESI’s Casting software.
Sand Casting
ESI’s Casting Simulation software enabled Suñer and DuritCAST to obtain accurate thermal and metal-flow predictions prior to tooling design. Process Engineers were indeed able to develop with confidence optimized risering systems for successful castings in a short period of time.
“We feel very confident with the simulation results obtained using ESI’s Casting Solutions”, said Luis Sierra, responsible for the automatic process control at DuritCAST. “We have even decided to refuse validating new mold designs if a simulation has not been carried out in advance”.
One of company goals of Faed for the coming years is to improve its productivity and limit the number of real prototypes. Faed has thus planned to simulate all its cast iron and steel components with QuikCAST, ESI’s fast and efficient solution for Casting Process Evaluation. Although Faed deals with massive components, weighing each several tons and measuring more than 5 meters long, the company is able to perform fast simulation in as little as a couple of hours. In addition, the new and powerful post-processing capabilities help foundry men to rapidly interpret results and track the porosities by scanning the entire component.
Grupo Fumbarri deals with cast iron components weighing up to 45 tons each and measuring more than 12 meters long. Using ESI’s Casting Solutions, Grupo Fumbarri is able to design complex shapes while delivering accurate results at each step of the casting process.
At San Eloy Fundiciones, mold filling never exceed 10 seconds and filling time is one of their key process parameters to reduce production time. With the recent use of simulation, they have already achieved the conception of new gating systems, increasing their productivity without increasing the risk of oxide formation, i.e. preserving the part integrity.
Die Casting
One of the major concerns with permanent mold applications is to monitor the die temperature during the entire process. CIE Automotive has been intensively using simulation for many years to design its die cooling devices, specifically for the pressure die-casting process. They now use ESI’s Casting Simulation software to model their semi-solid process with the SEED technology developed by Rio Tinto Alcan.
Investment Casting
Microfusión ALFA, major actor in the investment casting market, has been successfully using ProCAST for many years. Now the foundry has integrated the stress module in order to control the final shape, dimensions and stress concentration of their high quality components. This will help Microfusión ALFA make significant headway in their mold design to satisfy their customer’s requirements for tight tolerances.
Copper Alloy foundries
Cast iron, steel, aluminum and superalloys foundries are not the only ones to adopt simulation tools; copper alloy foundries are also seizing the opportunity. Casuso Propellers, producing large castings made of Cupro Aluminum for the marine industry, have recently equipped their foundry with QuikCAST and collaborated with ESI and Análisis y Simulación, to solve one of their main issues - the characterization of their material properties. By using the ProCAST reverse engineering capability, they were able to determine all the material properties needed to compare porosity prediction with experimental results.
“The use of ESI’s Casting solutions has become an essential decision tool that helps most of the Spanish and Portuguese foundries to get the right design while eliminating any risks,” declared Emilio Mencia de Miguel, Managing Director, ESI Spain.
For more information about QuikCAST and ProCAST, please visit: www.esi-group.com/products/casting
Análisis y Simulación is ESI’s trusted engineering partner for the sale, support and training of ProCAST and QuikCAST in Spain and Portugal. The company has over 17 years of experience in the implantation of solutions inside the foundry industry, including design and simulation of all process types (gravity, LPDC and HPDC) and employs over 60 high-level specialists covering different engineering areas.