During their 20-year lifetime, wind turbines must reliably operate under a wide variety of environmental conditions. Numerical modeling is essential for manufacturers to test their capabilities and to assess the risks of failure. Physical tests are expensive and only possible in limited circumstances due to the size of wind turbines and the lack of control of the wind conditions. ESI offers virtual prototyping software and services helping wind energy companies address these challenges and understand the intricacies of design and the interactions of the sub-systems during the different environmental conditions as well as the physics of the materials to manufacture components in a cost-efficient way.
Mechanical Components Reliability
ESI’s solutions enable the dynamic simulations of the mechanical system (gearbox, transmission), accounting for the flexibility of the supporting structure. It allows you to predict the lifetime and the risk of failure for what represents the first cause of loss of windmills.
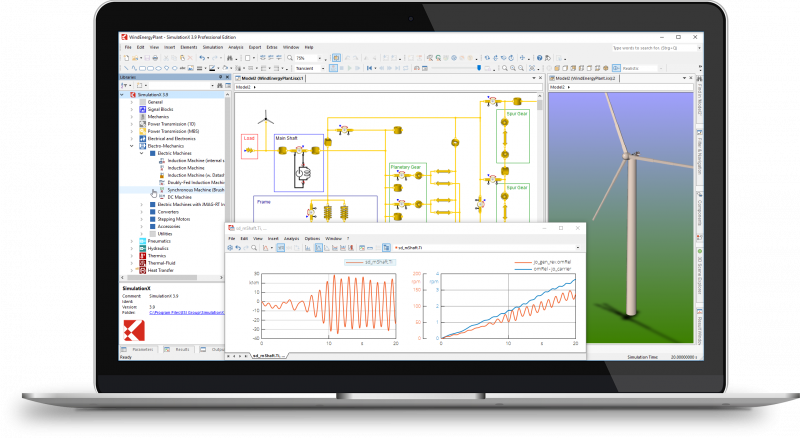
SimulationX allows us to optimize the wind turbine’s gearbox and drivetrain components to reduce dynamic loads, which in turn increases reliability and availability of the wind turbine.
Stefan Schemmert, Research & Development Eickhoff Antriebstechnik
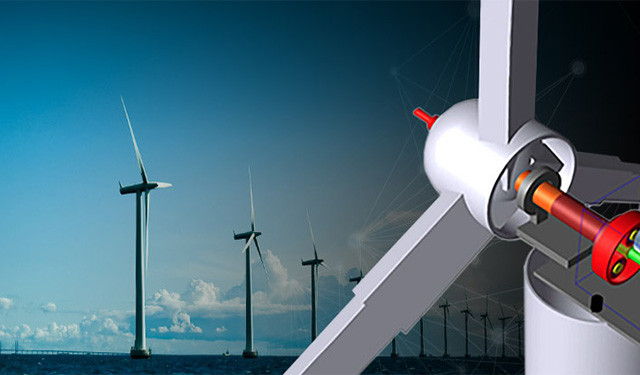
Reaching the optimal health monitoring for wind turbines and reducing operation and maintenance costs while ensuring a high level of performance remains the biggest challenge for Wind Farms. Today, new approaches allow you to relieve remaining gaps (data availability, representatively, physical behavior) and address each farm's specificities.
In this webinar, we highlight how coupling physics-based model with data analytics and machine learning enriches turbine monitoring and opens new fields for Wind Farm owners in their predictive maintenance strategy.
Noise of Windmills
Radiated noise is a primary concern when planning wind turbines, including sound produced by the blades as well as the noise emitted from the nacelle. ESI solutions offer a wide range of modeling options [CFD with moving components, SEA (Statistical Energy Analysis), FE (Finite Element), BEM (Boundary Element Method) and hybrid FE/SEA (Finite Element/Statistical Energy Analysis)]to determine near and far-field radiation from panels and openings.
Manufacturing of Very Large Blades
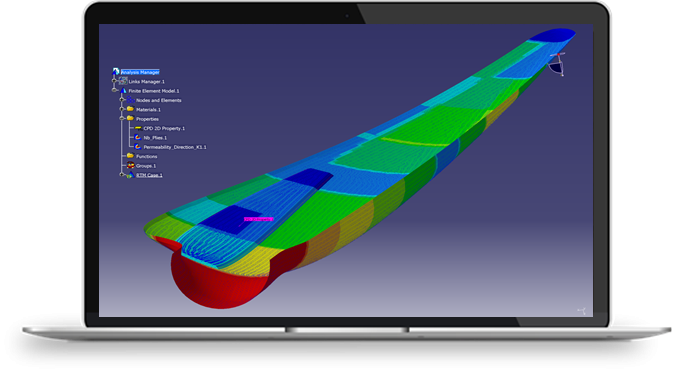
With the continuously growing dimensions of windmills, the manufacturing of unusually large blades has become a monumental challenge for the industry. The traditional physical trial-and-error process is becoming financially inefficient. ESI’s Virtual Manufacturing solution offers a practical alternate approach to optimizing the manufacturing of these large blades with Resin Transfer Molding. It provides the means to define an optimum injection strategy.
Natural Wind Conditions
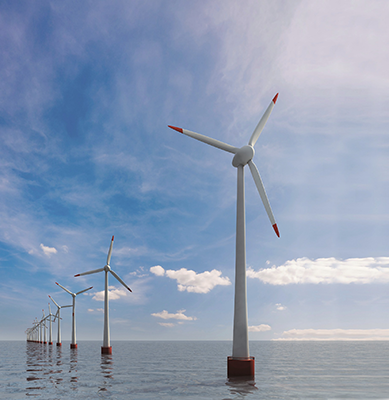
Power fluctuation is one of the main issues connecting wind farms to the power network. While an increasing number of utilities are requesting from the manufacturers to provide clues about the level of fluctuations, these can usually only be provided after testing full-scale prototypes in real wind conditions. ESI has developed a numerical natural wind model that matches the statistics of wind profiles and wind gusts that can be applied to realistic models of the windmills to predict the power fluctuations before manufacturing a prototype.