鋳造解析ソフトウェア ProCAST導入事例 日信工業株式会社
日信工業株式会社様の事例をご紹介します。
鋳造解析ソフトウェア
使用ソフト:ProCAST
日信工業株式会社 開発本部 芦田克彦氏、中島昇吾氏、伝田昌弘氏に(写真右から順)、鋳造による製品開発の特徴と困難、そしてProCAST導入の経緯と効果について詳しく聞きました。
日信工業株式会社 について
日信工業株式会社では、主に自動車、二輪車のブレーキ装置およびアルミ強度部品の開発、製造、販売を行っています。主要取引先は本田技研工業、トヨタ自動車、ダイハツ工業、スズキ、ヤマハ発動機、いすゞ自動車、川崎重工業、富士重工業、三菱自動車工業、ハーレーダビッドソン、トライアンフなど。設立1963年、年商2278億円、従業員数10,592名です(※ この事例に記載している財務関連の数字と事実は制作時、取材時点の2016年3月時点で公開されている情報に基づいています)
日信工業の製品について
-日信工業ではどんな製品を作っていますか。
日信工業のアルミ製品の概略は次のとおりです。
-
主な製品
自動車、二輪車のブレーキ装置およびアルミ強度部品 -
主な製造方法
アルミ重力鋳造他、ダイカスト・低圧鋳造など -
製品の大きさ
5cm四方から30cm四方 (※ 製品例)
-
出荷数
年間「数百万個」 / 月間「数十万個」
※1万個/ 日を越える工場もあります -
一個の鋳造の所要時間
数十秒~数百秒
※溶融金属を注ぎ、それが凝固するまでの時間
過酷な使用環境、多くの制限
-ブレーキをはじめとする御社製品開発の難しい点を教えてください。
困難は多くありますが、そのうちいくつかを列挙すると次のようになります。
-
「ブレーキ周辺は、自動車の『熱的に最も過酷な場所』のひとつ」
ブレーキとは「摩擦力を使って車軸の回転を止める装置」のことです。この場合、摩擦力はほぼすべて「摩擦熱」に変換されるので、ブレーキをかけると装置の周辺は非常に熱くなります。ちょっとした峠を下れば、200〜300℃の高温になります。またブレーキ装置は車体下部に露出しており、泥水、雪、塩水などに直接さらされます。外気に直接触れるため、ブレーキ使用時と非使用時の温度差も大きくなります。自動車内部で熱的に最も過酷な場所は「エンジン内部」ですが、二番目はおそらく「ブレーキ周辺」だと思います。
摩擦熱をもつブレーキ周辺 -
「ブレーキは絶対に不良があってはならない場所」
「クルマを止める」というブレーキのはたらきは、クルマの安全を確保するための「最も基本的かつ重要な機能」です。安全を第一義として究極の選択をするならば、クルマは「走らないことはギリギリ許されても、止まらないことだけは絶対に許されない」といえます。どんなに過酷な状況でもブレーキは必ず作動しなければいけません。 -
「ブレーキの『音』は、クルマの体感品質を左右する 」
自転車で急ブレーキを掛けると「キーキー音」が生じますが、この「ブレーキ鳴き」が自動車やオートバイで起きると運転していて情けない気持ちになります。クルマは移動の手段であると同時に、運転する楽しみをもたらすもの、あるいは人生を豊かにする財産、ステータスとなるものです。運転するお客様にご満足いただくためにも、ブレーキは静粛に動作する必要があります。 -
「外観デザインが重要になることも 」
自動車の場合、ブレーキ装置は車体下部の見えない場所にありますが、二輪車では車軸まわりの、割合に目立つ場所にブレーキが露出しています。外から見えるということは、デザイン性が重要になるということです。特に二輪車は近年、「趣味性の高い乗り物」となっており、それだけデザインは重要性を増しています。二輪車ブレーキ周辺 -
「薄くしたい設計側、厚くしたい製造現場」
車体を軽量化すれば、高燃費が実現するので、「なるべく小さく軽くあること」が求められます(だからブレーキの材料は、重い鉄製から軽いアルミ製に変わりつつあります)。またデザインの観点から見ても、一般的には、ボッテリ厚いよりはシャープに薄い方が格好良いといえます。ということは設計側とすれば、製品形状を、なるべく小さく薄く、シャープにしたくなります。
しかし鋳造製品の場合、強度と鋳造性の向上を実現するには、基本的には「肉厚」の方が良いのです。肉厚の方が湯が良く流れて、金型の隅々まで行きわたるので、不具合も生じにくくなるわけです。
このように「薄く小さくしたい」設計側と、「できれば厚くしたい、肉を盛りたい」製造側では基本志向にズレがあります。このズレは、開発段階で適切に解消する必要があります。 -
「要求仕様はあるが、自由度は高い 」
アルミナックル等は自動車メーカーからの依頼に応じて作ります。しかし、メーカーから指定があるのは「ナックルと他の部品が接する『取付点』の位置と形状」「材料」「重量」「強度・耐久性」などの仕様のみです。
これは逆にいうと、「要求仕様を満たしていれば、それ以外は 自由に創意工夫してよい」ということです。良い提案はもちろん歓迎されます。特に「軽量化」につながる案はお客様に喜ばれます。
自動車メーカーが求める難しい仕様をすべて満たし、その一方で「作りやすさ」も確保すること、それが日信工業側の「腕のみせどころ」になります。
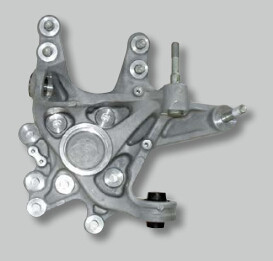
「良い鋳造」を一言で表現すると
-アルミ重力鋳造で製品を作る場合、どんな鋳造が「良い鋳造」ということになるでしょうか。
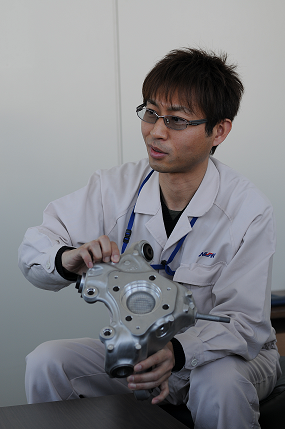
開発本部 開発管理室
長野管理・知財・CAE BL 研究員
伝田 昌弘 様
一般論としてブレーキのような大量生産品では、「寸法、重量、強度など各種仕様が設計通りに実現できる」「それを高い歩留まりで生産できる」というのが「良い製造」です。簡単にいえば「設計通り、確実にたくさん作れる」ということです。
では、この「良い製造」を実現するための「良い鋳造」を弊社のアルミ鋳造に当てはめていくと、以下のようになります。
強度を保証するためには、まず上述のとおり、設計図面通りの形状のものを作ることが必要で、さらに内部の欠陥が生じないように 「金型に上から注いだ湯が、湯口から遠いところから順々に凝固していき、最後は湯口のそばで固まって終わる」 ことが必要です。
そして、方案部分の体積を必要最小限にすることで、歩留まりの向上が実現できます。
しかし、この「良い鋳造」に対しては、「鋳造は、内部の観察が難しい」ということが実現の阻害要因となります。
鋳造は金型内部の現象を観察しにくい
- 「鋳造は、内部の観察が難しい」とは具体的には。
第一に鋳造の場合、「プロセスが始まると途中で止められない」ということが観察しにくさの一因となります。
たとえばプレス成形の場合であれば、加工途中で機械を止めて、仕掛品の様子を観察して…ということが可能かもしれません。
しかし鋳造の場合、「金属の凝固過程を途中で止めて様子を観察する…」ということは不可能です。
第二に鋳造には「不具合が外から分かりにくい」という困難もあります。ヒケ巣やブローホールは「内部の不具合」なので、外から観察しても分からず、後工程で機械加工を施した時に表面に露見することがあります。
特にブレーキ部品は液圧のかかる部品で、内部に欠陥があると液漏れにつながるため、絶対にあってはならない不具合です。
これは製品の最終検査を難しくする原因の一つとなります。鋳造物の品質検査は基本的には非破壊検査ですが、場合によっては何点か抜き取って、切断して中を見る、という破壊検査を行うこともあります。
この「内部を簡単に観察できない」という困難に対処するための施策の一つが、「ソフトウェアによる鋳造シミュレーション」です。コンピュータ内の
シミュレーションであれば、プロセスを止めることも内部を見ることも可能です。
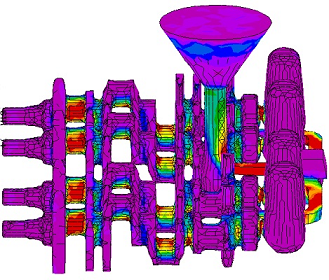
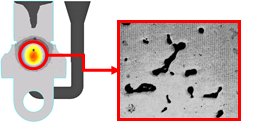
鋳造シミュレーションを始めた経緯
-日信工業がソフトウェアによる鋳造シミュレーションを本格導入したのはいつ頃からですか。
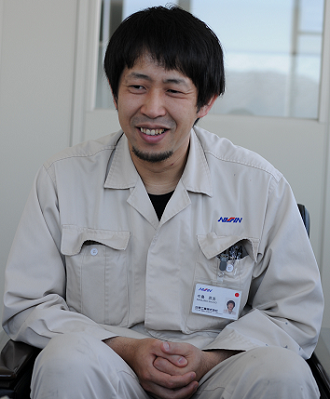
開発本部 開発管理室
長野管理・知財・CAE BL 研究員
中島 昇吾 様
弊社が、鋳造製品の開発にシミュレーションを導入したのは、今から十数年前、2002年頃からです。
それ以前は、大きくは「熟練者の経験と勘」「試作過程の試行錯誤」に依存していました。しかし、次第に部品形状・仕様の多様化、開発期間の短期化など、製造の前提条件が厳しさを増してきました。
同じような部品をずっと作り続けるのであれば、その過程で得た「経験と勘」が有効に使えます。しかし製造物が多様化してくると、それが難しくなります。
そこで開発スピードの向上、試作数の削減を目指して、鋳造シミュレーションを本格導入することにしました。つまりコンピュータの仮想空間の中で、形状や各種製造条件を変化させながら、金型内の湯流れ、凝固過程を観察するわけです。
なお、当時は初めて導入するにあたり、操作性・費用の観点から他社製品(以下 製品A)を導入しました。
ProCASTを選択した理由
-今回、製品AからProCASTに切り替えた理由は何ですか。
製品AからProCASTに切り替えた理由、逆にいうと「ProCASTが製品Aより優れている点」は、大きくは次の2点です。
-
有限要素法を使うことで高精度な解析ができる
-
ProCASTは湯流れと凝固を強連成で計算できる
「曲面を曲面として解析できる」
-優位点1.「有限要素法を使うことで高精度な解析ができる」とは具体的には。
鋳造シミュレーションによる正確な不具合予測のためには、金型内部の湯流れを正確に解析する必要があります。当社の製品は大部分が曲面で構成されていますが、差分法を用いた製品Aでは、曲面は微細な立方体の集まりで表現され、曲面上の湯流れはタテ・ヨコ方向に近似されてしまい、正確に再現できているとは言い難い状況でした。
一方、有限要素法を用いたProCASTでは、形状再現性の高い四面体・六面体メッシュを用いているため、境界が滑らかで湯流れをスムーズに再現することが可能でした。正確な鋳造シミュレーションを行うには、有限要素法で計算する方がより適しているという結論に至りました。
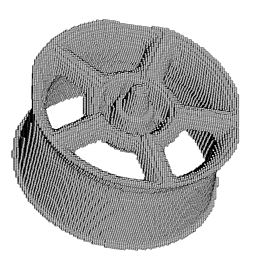
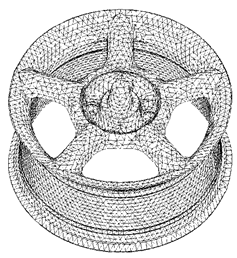
また、複雑な形状の部品を鋳造する場合、金型内部に「肉薄の部位」と「肉厚の部位」が生じます。薄い部位は、湯が流れにくいので、特に念入りに計算、解析する必要があります。
しかし製品Aは、直交格子メッシュを用いているため、精度が必要な箇所のみを細分化するといった、細かい制御をすることができず、その部分を含む列全てが細分化されてしまいます。結果、要素数が過大となり、精度向上の分以上に計算時間が長大化する原因となってしまいます。
一方で、ProCASTでは有限要素メッシュであるために要素分割の粗密の自由度が高く、計算精度が必要な部分のみ細分化したメッシュを生成することができます。これにより必要な計算精度を適切な計算時間で実行することができます。
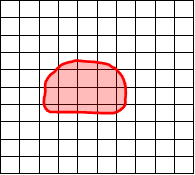
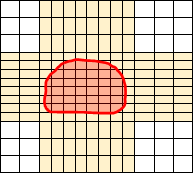
「湯流れと凝固を連成計算できる」
-優位点3.「ProCASTは湯流れと凝固を強連成で計算できる」とは。
製品Aでは、湯流れと凝固は別モジュールで計算する仕様でした。しかし実際の鋳造では、湯は、低温の金型に流れこむと同時に凝固し始めるので、湯流れと凝固は同時に解析できる方が再現性が高いと言えます。
例えば、ナックルのような、比較的大型の鋳造をする場合、充填が完了する前に端部の温度は凝固点以下に冷却されていることがあります。
そのような状態で、凝固モジュールに受け渡しても、正確に凝固計算されず、結果として欠陥の予測ができなくなってしまいます。
ProCASTでは、湯流れと凝固を同時に計算できるので、前述のような現象が起きた場合も欠陥を正確に予測することができました。

シミュレーション導入による効果
鋳造シミュレーションを導入する前は、不良率が比較的高く、良品のみを選択して出荷する状況があり、お客様に心配をおかけすることがありました。昔はそれでも問題になることはありませんでしたが、生産量の増加・多品種化となった今、高精度なシミュレーションがなければ、現在のように不良率を低下することはできなかったと思います。
今後の期待
-日本イーエスアイへの今後の期待をお聞かせください。
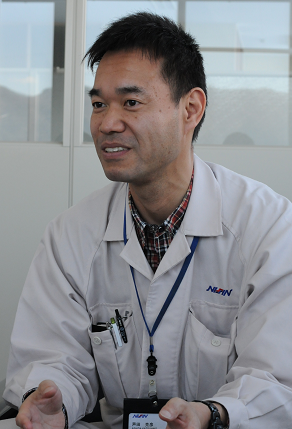
開発本部 開発管理室
長野管理・知財・CAE BL 主幹
芦田 克彦 様
今では、開発プロセスの中でシミュレーションによる生産性評価でOKを得なければ、出図承認を得られない体制となっています。それほど、ProCASTでのシミュレーションを信頼しているということです。
日信工業では、今後もさらに高品質の鋳造製品を製造していく所存です。
弊社のこの取り組みにご協力いただきたく日本イーエスアイには、解析精度のさらなる向上などソフトウェアのアップデートを継続していただけることを期待します。
例えば、長尺物の鋳造プロセスで発生する、曲がり・反りなどの変形予測は現在でもある程度できますが、最終形状にこの曲がり・反りを見込んだ金型形状を予測することができるようになれば良いですね。
今後も優れた製品とサポートを通じて、より一層の後方支援を期待します。
今後ともよろしくお願いします。