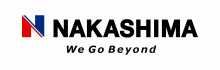
PAM-COMPOSITES 導入事例 ナカシマプロペラ株式会社
ナカシマプロペラ株式会社様の事例をご紹介します。
複合材成形解析ソリューション
使用ソフト:PAM-COMPOSITES
ナカシマプロペラ株式会社 コンポジット事業部 部長 山磨敏夫 氏(右側)、課長 櫻井貴哉 氏(左側)にPAM-COMPOSITES/PAM-RTMモジュールを導入した経緯とその効果について詳しく聞きました。
ナカシマプロペラについて
ナカシマプロペラは船舶用プロペラを開発・製造している企業です。一般商船用プロペラでは国内シェア70%で第一位。
世界でも30%でトップクラスのメーカーです。年商240億円、社員数380名、設立1926年。
商船向け炭素繊維複合材料製プロペラを世界で初めて商用化
― ナカシマプロペラで今注力されている、「炭素繊維複合材料によるプロペラづくり」に関して、まず現在の炭素繊維複合材料製プロペラの製造・販売状況を教えてください。
ナカシマプロペラでは炭素繊維複合材料のプロペラづくりを自社の次世代技術と位置づけて、2007年から研究開発を開始し、東京大学など研究機関と共同研究を続け、2015年には「世界初の商用化」を実現しました。2017年現在も商船向けの炭素繊維複合材料製プロペラを商用製造できるのは世界で弊社だけです。

プロペラで使う炭素繊維複合材料は「炭素繊維強化プラスチック(CFRP)」です。 船舶用プロペラでは最も大きい物がタンカー用の直径10メートル級プロペラとなり ますが、CFRPプロペラでは現在、最大で直径4.2メートルのものが製造可能です。 現在の年間製造数は約10個。現在、日本の内航船の製造数は年間100隻程度なので、 うち1割にCFRPプロペラが出荷・搭載されていることになります。 CFRPプロペラは材料費も製造費用もまだまだ高価ですが、今後コストダウンを進 めることにより、さらに多くの製造数、出荷数が実現できるものと見込んでいます。
良いプロペラの3条件
― CFRPプロペラは従来のプロペラに比べ、どんな点が優れているのでしょうか。
まず、構造的な観点での「良いプロペラとはどういうプロペラか」という部分からご説明します。良いプロペラでは大きく「耐久性」、「軽量(低振動)」、「正確な形状」の3点が重要な要素となります。
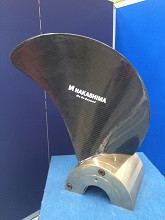
要素1.「耐久性」
船舶、特に外洋を航行する大型船舶の場合、プロペラは非常に長期間、連続運転します。大型タンカーでは航行期間は1 ヶ月に及びますが、これは直径10メートルの大型プロペラが1 ヶ月間(720時間)、休み無く回り続けることを意味します。この前提を考えた場合、プロペラには当然、高い耐久性が求められます。
要素2.「軽量(低振動)」
一般に乗り物では「軽量は高燃費につながるから良い」となることが多いのですが、プロペラは船舶全体の重量に比べて非常に小さい部品なので、これを軽くしても直ちに高燃費につながりません。
むしろ水中を高速回転するプロペラでは、軽量であることのメリットは「低振動」の方です。まず低振動であれば船の内外で騒音が小さくなります。また脈動するエンジン回転では、軽量である方が回転がスムーズになるのでエンジンの負荷が低減します。この負荷低減効果は、荒天で海が荒れている中を航行するとき特に重要になります。
要素3.「正確な形状」
長期間連続運転が前提となるプロペラでは寸法精度がわずかに違うたけでも、エンジンの性能や耐久性に大きな影響を与えます。プロペラの製造では、直径10メートルの大型プロペラでも寸法の公差は1%以内で正確を期します。また表面の平滑度に関してはミクロン単位で管理します。
炭素繊維は高強度で軽量な素材なので、ここまで述べた3要素のうち耐久性と軽量(低振動)を実現するために優れた材料といえます。ナカシマプロペラは次世代の主力製品として炭素繊維とプラスチックを合わせたCFRPプロペラに注力しています。
炭素繊維複合材料に着目した理由
― ナカシマプロペラがCFRPプロペラの開発に着手した経緯を教えてください。
通常のプロペラは、銅合金を鋳造して作ります。ナカシマプロペラの売上げも大部分は銅合金プロペラに依っています。しかし弊社では2つの理由から、「炭素繊維のプロペラづくりに着手すべき」と考えるようになりました。

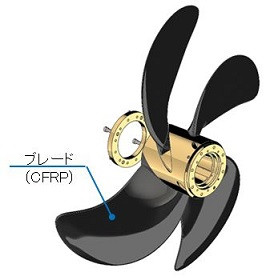
1つめの理由は「銅資源の枯渇」です。銅はすでに希少鉱物資源となっており、材料費は年々高騰しています。この先、銅の供給状況が好転する見込みは薄いと思われます。将来に備え、炭素繊維複合素材によるプロペラ製造の技術を確立するべきと考えました。
2つめの理由は「複合素材メーカーの潜在的脅威」です。現在、弊社は船舶用プロペラの分野では国内外で高いシェアを取れています。しかし将来的に炭素繊維など複合材の材料コスト、製造コストが低下したとき、「複合素材メーカーがプロペラ業界に進出してくる」こともありえます。その潜在的脅威に抵抗するためにも炭素繊維複合素材のノウハウを蓄積しなければならないと考えました。
そして2007年に研究開発に着手し8年間の試行錯誤を経た後、2015年にはついに船級承認を得て一般商船向けの商用化を実現できました。
炭素繊維複合材料製プロペラの製造工程
― 炭素繊維複合素材を使ったCFRPプロペラはどのように製造するのでしょうか。
CFRPプロペラは真空含浸成形(VaRTM)により、炭素繊維に樹脂を含浸・硬化させて作ります。以下、CFRPプロペラとしては現時点で最大となるブレード径約2メートル(プロペラ直径4メートル)の物を例にして説明します。
CFRPプロペラのVaRTM成形プロセスは、次のとおりです。
-
「炭素繊維を重ねてブレード形状を作る」
裁断した炭素の場合、炭素繊維の層の数は厚い部位で数百枚、薄い部位で十枚程度となります。 -
「フィルムとフローメディアで炭素繊維を覆う」
ブレード大の炭素繊維を、『フローメディア』と呼ばれる樹脂の流れを制御するための網目状のシートで覆います。さらにその上をフィルムバッグで覆います。 -
「フィルム内部を真空にして、素材を密着させる」
フィルムバッグ内部の空気を抜いて、真空圧により、炭素繊維の層、フローメディア、フィルムを相互に密着させます。 -
「樹脂を含浸させる」
真空圧を使って、配管からフィルムバッグ内部に樹脂を流し込みます。樹脂が炭素繊維層の全体に行き渡るまで約3時間かかります。 -
「樹脂を硬化させる」
所定の硬化プログラムにそって加熱し、樹脂が固まったところで含浸成形のプロセスは終了となります。
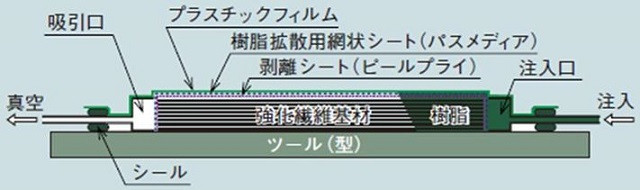
炭素繊維および成形法
![]() |
![]() |
製造上の困難
― 含浸成形によるプロペラ作りでの製造上の課題、困難について教えてください。
開発に着手した当初は銅合金の鋳造のノウハウはあるものの、炭素繊維複合材の含浸成形については全く未知の分野、ゼロからのスタートとなりました。その後、東京大学と共同研究を重ねてノウハウを得ていきましたが、基本的には「試行錯誤と手探り」で開発を進めたことになります。
含浸成形では、「炭素繊維層の空隙に隈なく樹脂を行き渡らせるプロセス」が製造上の難点です。鋳造でも含浸成形でも、その理想状態は「素材が型内部で隅々まであまねく均等に行き渡り、均等に固まる」ことです。しかし含浸成形の場合、型内部に炭素繊維の固まりがあるためそれが障害物となり、「樹脂素材を均等に行き渡らせること」が難しくなります。
プロペラ完成品と炭素繊維層は形状も見た目体積も同じです。しかも炭素繊維層は含浸前に真空圧でしっかり固められます。こう聞くともはや樹脂が浸透する隙間など無いような気がしますが、実は完成品プロペラの炭素繊維部分と樹脂部分の体積比は6:4です。
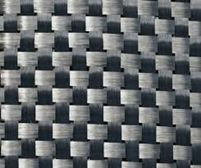
つまり、真空密着させてもなお残る炭素繊維層の間の空間、そして炭素繊維の織目部分の空隙は、一つ一つは微少であっても、すべてを合計すると全体の4割に及ぶということです。
炭素繊維への樹脂の含浸は、「流し込む」というスピーディな言葉とは対極の世界です。繊維の織目の微細な隙間にじっくりじんわり根気よく浸み込ませる、そんな工程となります。
ここまで述べた前提条件があるため、炭素繊維複合材の含浸成形で、「繊維の内部に隅々まであまねく均等に樹脂を行き渡らせ、均等に硬化させる」という理想像を実現するのは非常に難しくなります。
「 経験と勘」から、シミュレーション導入へ
― そうした困難にはどう対処していたのでしょうか。
正直なところでいうと最初は「経験と勘」で何とかしていました。しかし受注が好調になり、製造するプロペラのサイズが大きくなると、経験と勘だけでは対処が難しくなってきました。
炭素繊維複合材の場合、失敗すると高価な炭素繊維がムダになります。大きなサイズのプロペラを、コスト、納期、品質を確保しながら安定生産するには、経験と勘だけではやはり限界があると悟りました。
そこでシミュレーションソフトウエアを導入し、コンピュータ内部で含浸成形を再現し、試行錯誤は極力コンピュータ内部で行うよう方針を転換しました。いくつか候補製品を比較検討しましたが、PAM-RTMが「射出成形だけではなく、3次元でのVaRTM成形シミュレーションにも対応している点」、「東京大学をはじめ国内で多くの導入実績がある点」で他製品に比べ優っていたので、これを採用しました。
PAM-RTMを使った含浸シミュレーション
― 現在、PAM-RTMの活用ではどんなパラメータを変えてシミュレーションしているのでしょうか。
大きくは「注入配管の数、位置」、「フローメディアの大きさ、位置」の2点です。
何十、何百層もの炭素繊維に樹脂を浸み込ませる場合、「ブレード表面と平行な方向(積層した繊維シートに沿った方向)への樹脂の浸透」と「表面と垂直な厚み方向への樹脂の浸透」の2つの方向で樹脂流動抵抗に大きな差があるため、これら2つの方向について制御する必要があります。
うち前者については、『フローメディア』と呼ばれる網目状のシートをフィルムと炭素繊維の間に配置し、これにより樹脂の浸透を促進、制御します。後者の厚さ方向への浸透については、樹脂を注入する配管の数、位置、径を変えることで、含浸状態を制御することになります。
PAM-RTMによるシミュレーションでは計算時間は約3時間です。
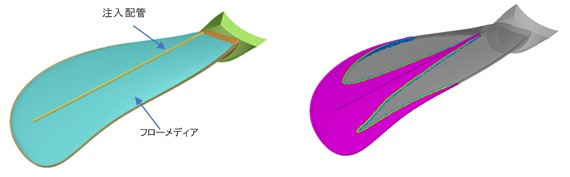
※掲載している解析画像は、一例であり実際の製造プロセスに適用したものではありません。
PAM-RTMの導入効果
― PAM-RTMの導入効果を教えてください。
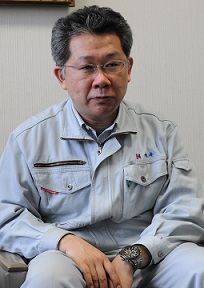
コンポジット事業部 課長 櫻井貴哉氏
PAM-RTMによるシミュレーションを導入したことで、まず試行錯誤に要する時間とコストを削減することができました。たとえば従来の経験と勘の時代には、3回実製造して3回とも失敗し、4回目でやっとOKになっていたのが、事前にシミュレーションを行うことで一発で成功できたという事例もありました。実製造での失敗は炭素繊維、樹脂、製造工数がすべて無駄になることを意味しているので、コスト削減効果は多大です。
また実製造で失敗したときに、その原因を事後シミュレーションを通じて分析、検証することが可能になりました。シミュレーションの結果値と、実物の検査値を照会することにより、樹脂が炭素繊維の空隙部分で含浸する状態を子細に把握、予測することが可能になりました。
現在は、PAM-RTMの活用により、製造における失敗と成功の理由、因果関係を詳細に把握することが可能になり、単なる結果オーライではない、根拠を持ったノウハウが着実に社内に蓄積されています。
PAM-RTMの導入、活用により、製造プロセスの仮説・検証のスピード、PDCAサイクルを回す速度と精度が向上したといえます。
初期の注入配管、フローメディアでの解析結果 |
解析結果により配置変更し、含浸完了時間を短縮 |
プロペラブレードでの樹脂含浸解析による改善
※掲載している解析画像は、一例であり実際の製造プロセスに適用したものではありません。
先行ユーザーからのアドバイス
― 炭素繊維複合素材による製造プロセスの改善に、ソフトウエアによるシミュレーションを導入することを検討している企業担当者に向けて、アドバイスなどあればお聞かせください。
CFRPプロペラの製造も商用化しても最初の1年ぐらいは経験と勘でしのいできました。しかしあるとき製造で「たぶん上手くいくだろう」と思ってやったことが3回連続で失敗してしまいました。こうなると社内の品質管理部門からもクレームが来ますし、自分たちとしても悔しいですし、ちょっと焦るわけです。
しかしこういうときは、失敗の原因は、小手先を少し変えれば何とかなるという話ではなく、何かが根本的にダメなんですね。その根本的な原因が何かを調べないことには前に進めないわけですが、ただこれは実際の材料、設備を使って調べるとなると手間もコストも大変なことになるわけです。
でもシミュレーションソフトウエアなら手間やコストを気にせず、自由に大胆に試行錯誤ができる。そういう便利さは一つの魅力かなと感じています。
今後の期待
― PAM-RTMおよび日本イーエスアイへの今後の期待をお聞かせください。
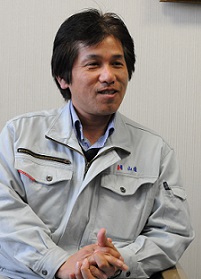
コンポジット事業部 部長 山磨敏夫氏
ナカシマプロペラでは次世代の主力技術として、炭素繊維複合素材によるプロペラ作りをさらに推進していきます。PAM-RTMはその取り組みの中で欠かすことのできない道具になるでしょう。引き続き、優れた製品とサポートを通じて、ナカシマプロペラのプロペラ作りを後方支援していただくことを希望します。今後ともよろしくお願いします。
複合材成形解析ソリューション
使用ソフト:PAM-COMPOSITES