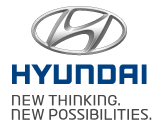
Hyundai Motor Company develops a dummy model to virtually test seat vibrations
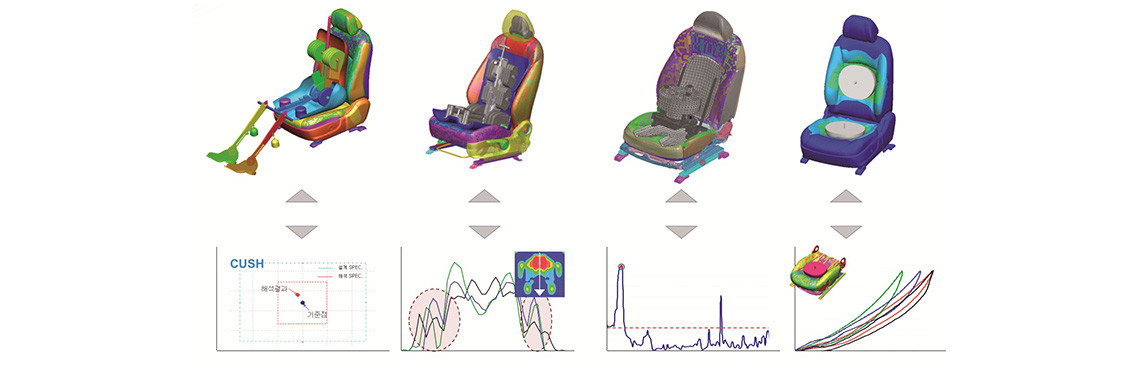
Since seats contain lots of components, it's very difficult to find the factors that influence the dynamic comfort of the seat. We tried to figure this out using VIRTUAL SEAT SOLUTION and reached our goal. This new way of working will help us save money and time effectively.
HAN, JI WONBody & Trim development team
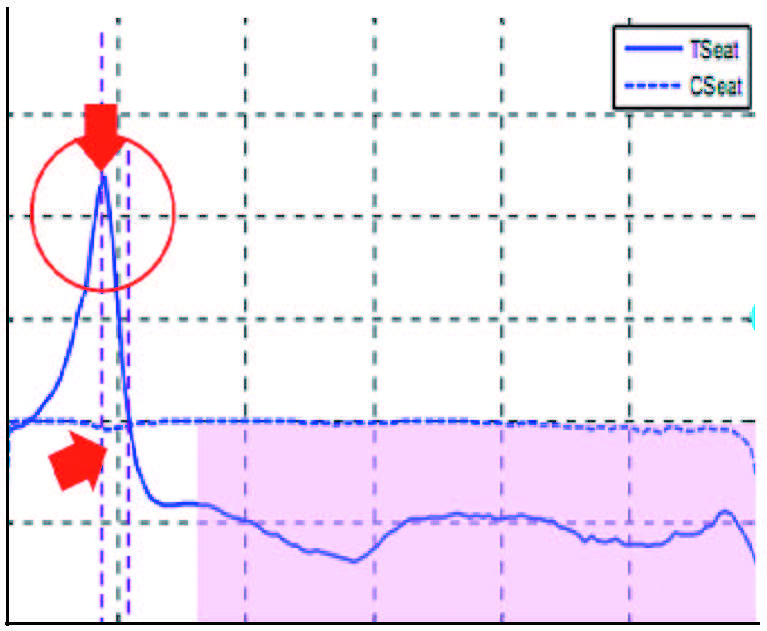
Seat occupant comfort is impacted by vibrations; this constraint must be taken into account during the seat design process. Therefore a reliable test has to be defined. Hyundai Motor Company originally uses Virtual Seat for checking the occupant’s posture in the seat, the body pressure and the foam hardness. The challenge of this project, performed by Body & Trim development team, is to develop a virtual dummy model and to perform accurate virtual vibration tests. (main image banner).
With the fully validated dummy model, Hyundai Motor Company can now perform virtual vibration testing with VIRTUAL SEAT SOLUTION earlier in the development process. By seating first the dummy and taking into account foam compression and induced dynamic properties at each point of the seat, the virtual vibration test is accurate and can replace some of the physical prototypes.
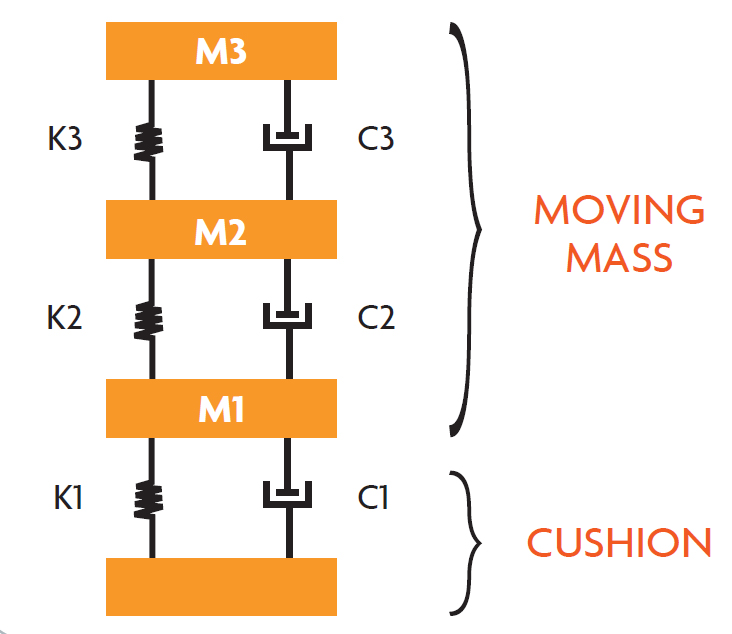
Impact of vibrations on seat occupant comfort
During long periods, more than two or three hours, of driving, a seat occupant feels an increase in muscle fatigue due to vibrations. Indeed, seat foam stiffness increases which reduces insulation. Through an analysis of the seat transfer function (fig. 2), Hyundai Motor Company engineers are able to improve seat design to decrease the discomfort originating from vibrations.
The seat must be designed in such a way that:
- the transmissibility at the natural frequency is reduced;
- the natural frequency corresponds to an area of less sensitivity for the human body;
- the transmissibility in the 8-30Hz range, which is related to long-term driving, is minimized as much as possible.
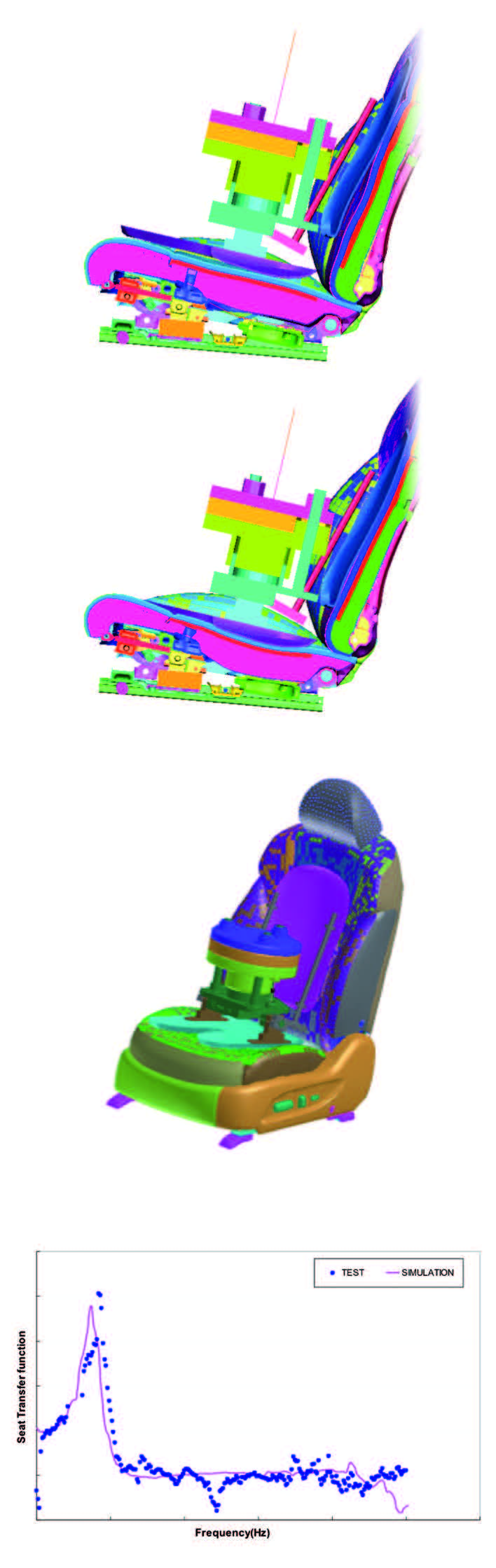
Difficulties with seat vibrations testing
Working with the seat transfer function is a good way to avoid the subjectivity of tests performed with human volunteers. Additionally, it is very difficult to obtain a good repeatability of measurement with human tests, since each individual human body has a particular intrinsic non-linear response, and any change in position will change the dynamic response. A seat transfer function obtained with a dedicated vibration test dummy is a solution to measure objectively the dynamic comfort of the seat. This vibration test dummy uses a moving mass and actuator system to have the similar characteristics to a human vibration response.
Development of a Finite Element dummy model
To virtually perform vibrations tests, a dummy model had to be developed. The geometry of the physical dummy was first captured and meshed, then a spring-mass system with multiple degrees of freedom was developed (Fig. 3). For each sub-component of the physical dummy, the transfer function was
measured, and the Finite Element dummy model was tuned accordingly. The springs’ stiffnesses were adjusted from the natural frequency and the damping coefficients from the amplitude of the transfer function at the natural frequency.
The Finite Element dummy model alone was then validated by comparing for each of its components the accelerations during several vibration tests with the physical ones. The transfer function of each sub-component was also measured and validated. Such comparisons were performed with three dummy sizes: female 5th percentile, male 50th percentile and male 95th percentile.
Validation on industrial seat
After having correctly defined the system modeling for the Finite Element dummy and compared its dynamic answers to the ones of the physical dummy, a validation on an industrial seat was initiated. As shown in figure 4, the first step of this validation was the sitting of the dummy in the seat. This stage was mandatory as it set the right pre-loading conditions. It also determined the right dynamic properties, which are highly non uniform in the foam and dependant of the foam compression.
The second step was to simulate the vibrations test with the seated dummy and these chained properties to obtain the transfer function (pink curve in Fig. 4). As shown in the graph (Fig. 4), the model provided a good correlation with the physical prototyping (blue points in Fig. 4). The virtual vibration test is thus predictive enough and can replace some of the physical prototypes.
Story release date: March 29, 2013