
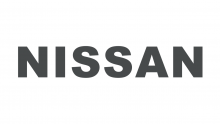
ESI助力日产在用于,更安全、更轻车辆的碳纤维部件生产方面取得突破
复合材料
地面交通
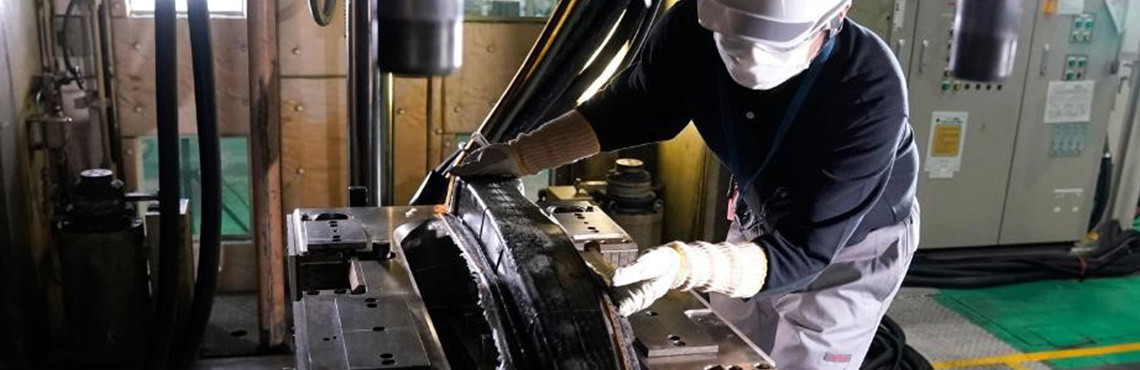
日产使用RTM(C-RTM)技术。这是一种复杂的复合材料制造工艺,在注入树脂时,冲压部分打开,以减少树脂在模具中扩散所需的时间。ESI PAM-COMPOSITES的使用使日产成功摆脱了反复试验,并通过实施新的模拟方法,使用预测性CAE重新定义了其C-RTM。因此,该团队成功地将制造周期时间大幅缩短了80%,这将支持碳纤维部件在轻型车辆大规模生产中的推广。
Rieko YamaguchiVehicle Manufacturing Element Engineering Section, Vehicle Production Engineering and Development Division at Nissan
故事
日产的制造工程师最近取得了一项技术突破,这将使该公司能够为批量生产的汽车推出碳纤维部件。碳纤维增强塑料(CFRP)属于性能材料,在保持相同强度和刚度的同时,能显著降低整车重量,但通常相关的复杂、漫长和昂贵的制造过程意味着它们只能用于跑车。
如今,日产正通过改进的压缩树脂传递模塑(C-RTM)工艺加快碳纤维汽车零部件的生产。
将预成型的碳纤维放入模具中,在压制(RTM)前注入树脂。C-RTM的一个特点是在注射树脂时,压模保持部分打开,以减少树脂在模具中扩散所需的时间和循环周期。不幸的是,波纹和干斑等缺陷依旧常见。在减少循环周期的同时掌握工艺和生产质量可能非常具有挑战性。制作压模也非常昂贵。
为了提高效率,车辆生产工程和开发部决定放弃传统的每个新零件通常需要三次物理试验的试错法。通过切换到CAE模拟,团队成功地将其工艺研发时间缩短了50%,并将单次成型时间缩短了80%。
ESI制造解决方案专门用于精确预测树脂将转移到哪个区域(树脂浸渍),允许工程师放置适当数量的凹槽以分布树脂,并重新考虑浇口和凹槽形状。CAE还帮助团队解决了与温度和固化速度相关的挑战,以及预测树脂流动的摩擦阻力。最终,该团队成功地将制造周期缩短了80%,并允许日产生产更复杂的零件形状,这转化为每辆车平均减重了80公斤。