VIRTUAL PERFORMANCE
SOLUTION
Software to Simulate Strength and Dynamics
Virtual in-operation try-outs, which allow for a wide range of simulated tests and experiments, play a pivotal role in achieving optimal vehicle performance and reducing warranty, recall, and maintenance costs. VPS enables engineers to identify potential weaknesses and flaws in the design early on, making it possible to make necessary adjustments before physical prototypes are built. This iterative process saves time and resources, leading to more robust and reliable car designs without incurring the expenses associated with physical testing.
With VPS, engineers get access to boundless testing capabilities to cover the most common, strength, dynamics, and misuse set-ups such as:
- Effectively assessing the stiffness of a complete vehicle, both, in its static state and during realistic driving scenarios, to achieve the right balance of strength, weight, comfort, and handling.
- Analyze the impact of road potholes on a vehicle, considering factors like tire physics and road speeds, and eliminate the costly physical replication of this test.
- Identify potential damage from forcefully over-opening doors and hoods, along with assessing the vehicle hood's stiffness against aerodynamic loads
- Simulate torsional stresses on a vehicle's structure, or body-in-white (BIW) during realistic driving scenarios.
- Panel slam analysis to predict the impacts of regular door slamming on structural integrity early.
Unique VPS Capabilities for Waterflow Testing
Here at ESI, we are combining the mesh-free Finite Point Method (FPM) with our structural dynamics solver Virtual Performance Solution (VPS) to simulate the interaction of the water with the car structure. This way, our customers can cover the complete range from tank sloshing and water drain applications for car closures through to full car water crossing including deformable tires and suspensions and soiling scenarios – accurately easily, and quickly – in one single software.
Joint, holistic simulation of vehicle water crossings
Shift away from separate analysis using CFD for water flow and FEA for deformation prediction towards one single simulation tool! Simultaneously study water flow and potential ingress as well as the impact of the water on the structure and body. Accurately predict flow, ingress, and structural impact at various speeds.
HONDA R&D has been using ESI’s Virtual Performance Solution for over 20 years. Today, we are leveraging the capacities of Virtual Performance Solution’s Single Core Model on a full car for our latest vehicle platform development…. not only for crash and safety domains but also for NVH and durability.
Eisei HiguchiiChief Engineer at HONDA R&D Co. Ltd
Accurately predict water intrusion using one single software
Find out how the seal might deform and allow water intrusion into the vehicle! Simulate the reaction between barriers such as seals and water, for example on wet surfaces, during heavy rain, or over pressure water spray. Shift away from separate analysis CFD for water flow and FEA for seal flex prediction towards one single source of truth.
Design more effective fuel tanks in ICE and next-generation hydrogen-powered vehicles
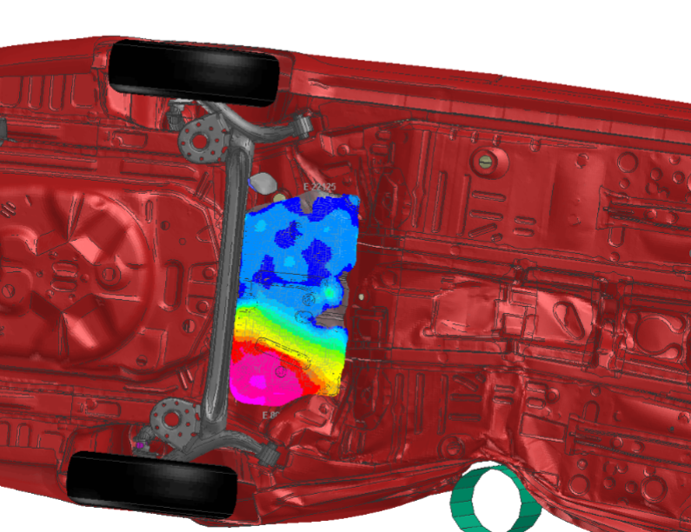
Realistically represent the sloshing of a liquid in a tank with the vehicle and predict both, the behavior of the liquid and its effect on the integrity of the tank itself! Simulate how the tank will distort or deform with the force of the liquid sloshing, either during vehicle use or a crash scenario. Shift away from disjointed analysis using CFD for fluid flow and FEA for tank physics assessment and move towards one single simulation environment.