ESI Unveils the Most Intuitive and Reliable System Simulation Software, SimulationX 3.9
Paris, France – December 14, 2017 – ESI Group is a leading innovator in Virtual Prototyping software and services for manufacturing industries, announces the release of ESI’s SimulationX 3.9, software platform for multiphysics system simulation. Designed for many industries – from automotive, energy, and mining to industrial machinery, railways, aerospace and aeronautics – SimulationX has proven to be one of the most reliable and customer-friendly solutions on the market. Customizable to each industry specific need, this new version of SimulationX is multitask and integrates the features necessary to support engineers in their day to day work.
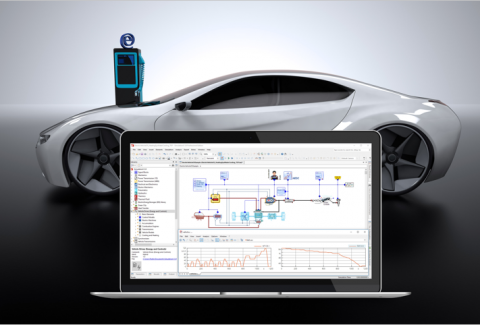
ESI’s SimulationX model of an electric vehicle including WLTP driving cycle, cooling system for the battery and the electric machine, as well as the cabin heating and a driver model.
SimulationX* is a simulation platform for physical analysis that addresses almost all machine and plant engineering disciplines. OEMs, suppliers, engineering companies, as well as research and educational facilities use SimulationX to make the right decisions during the concept phase for new products. The solution also supports in depth analysis of the system’s dynamic behavior and real-time-testing before the first prototype is built, as well as predictive operational steering. The enabling SimulationX modeling and simulation approach is optimized for complex Multiphysics systems, reliable analysis to be conducted with a minimal set of parameters and in short calculation time. Especially for extensive variation studies, this feature saves valuable time and opens doors to targeted system optimization.
Not limited to a specific application or industry, SimulationX is the most customizable solution available. ESI’s solution also benefits from a unique ability to communicate with other Computer-Aided Engineering (CAE) solutions such as Finite Element Method (FEM) simulation software, Model Based Systems Engineering, optimization tools, and real-time-platforms. Through convenient input assistants, it is easy for users to write their own model code based on the modeling language Modelica®**. It is as easy to use for simulation experts as well as beginners to tackle several challenges. Simulation engineers can now process the results of their work to quickly and easily retrieve all the information they need to make the right decision. ESI provides not only the platform and model libraries with comprehensive analysis methods but also associated engineering services.
Historically known as a proven solution with a focus on simulating physical systems, SimulationX 3.9 is making big strides towards providing a single modeling and simulation platform for complete, technical systems. By implementing the Modelica® Synchronous language elements, ESI’s software is now able to efficiently simulate synchronous circuits as used in almost all digital controls. With SimulationX, digital control structures can now efficiently be designed and tested in the same environment and in interaction with a model of the physical machine.
SimulationX 3.9 masters both comfort and efficiency in system modeling and simulation to offer maximum freedom to all users, including in the mining sector. For example, the new SimulationX belt conveyor library integrates the use of a novel approach for automated model setup and modeling of belt conveyor systems. Users who face specific analysis tasks can combine the belt conveyor models with proven elements from other SimulationX libraries, such as Power Transmission, Electro-Mechanics and Heat Transfer.
Linking the digital models of a belt conveyor's mechanical and electrical components in SimulationX produces a digital twin which allows for design optimizations and virtual commissioning of the belt conveyor. Parameters for converters and motors as well as complex controllers can be tested and chosen in advance to validate the technical performance and to minimize time and tests on site for a faster and safer commissioning process – something from which we benefit as much as our customers,” says Dr.-Ing. Torsten Hellmuth, Product Manager Bulk Material Handling, Siemens AG, Process Industries and Drives Division.
New features in SimulationX 3.9 allow engineers to navigate easily within complex model structures and conveniently set their necessary parameters. Along with improved calculation methods and results visualization, all main work steps have become faster: modeling, calculation, and analysis. This latest version addresses several challenges including higher performance while handling large models, as well as enhanced visualization, navigation features for the diagram view, and easier parametrization. The newly developed task manager enables flexible and powerful variant studies including parallel tasks with different simulation methods.
Through new model elements in the electro-mechanical and “Vehicle Drives (Energy and Controls)” libraries, simulation engineers can now solve reoccurring challenges around e-mobility on all levels. In addition to integrating e-mobility into sustainable and efficient energy grids, SimulationX also allows electric vehicles consumption analysis. This includes path dependent driving cycles, operation profile optimization and even detailed evaluation of electric components. These features, primarily designed for ground transportation and urban planning, combine the influence of thermal behavior, cooling systems on the energy consumption, along with battery aging simulations or electrical and electromechanical systems evaluation.
As a simulation solution for conventional drive trains, in use in the automotive industry for more than two decades and constantly refined, SimulationX has now reached another level of detail for vibration damper modeling. Along with the successful model elements parameterized through characteristic curves, SimulationX 3.9 introduces new elements describing dual-mass flywheels and engine mounts parameterized through design data, including their components. These can also represent frequency-dependent damping behavior in transient simulations.
Summarizing all new and enhanced functionalities and applications in the new version 3.9, SimulationX strengthens its position as the Modelica-based platform for modeling, simulating and analyzing complex, Multiphysics systems. Extended features for ease of use as well as expert modeling and simulation features, make it the tool of choice for design engineers and simulation professionals alike for a multitude of industries and applications.
*SimulationX is a registered trademark of ESI ITI GmbH
**Modelica® is a registered trademark of the Modelica Association
For more information about ESI’s SimulationX, please visit: www.esi-group.com/products/simulationx
Join ESI’s customer portal myESI to get continuously updated product information, tips & tricks, view the online training schedule and access selected software downloads: https://myesi.esi-group.com
For more ESI news, visit: www.esi-group.com/company/news
ESI Group – Media Relations
Delphine.AvomoEvouna [at] esi-group.com (Delphine Avomo Evouna)
+33 1 41 73 58 46