ESI Software Solutions Benefit the Biomedical Sector
Paris, France – April 2, 2015 – ESI Group, pioneer and world-leading solution provider in Virtual Prototyping for manufacturing industries, and partner of numerous R&D projects in the biomedical sector for many years, announces the results of technical studies recently carried out in France. These studies, performed in collaboration with a hip prosthesis manufacturer, have led to a better understanding of the issues related to the manufacturing, placement and in-vivo mechanical behavior of such prostheses. These studies clearly illustrate the potential for numerical simulation in the medical sector.
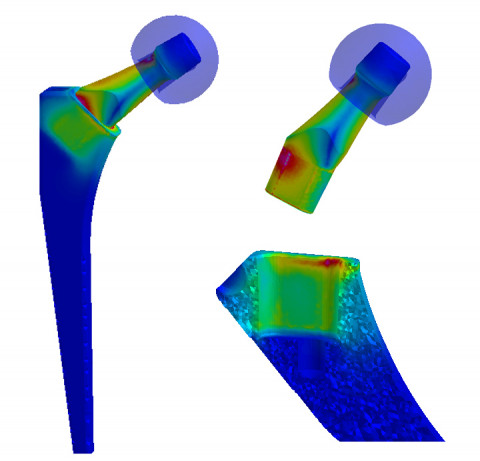
Simulation results in Virtual Performance Solution: mechanical stresses for a given load case.
The fitting of total hip prostheses is one of the top five operations in orthopedic surgery today; and such surgeries are steadily rising according to statistics from the French Hospital Information Technology Agency (ATIH)*. With patients - especially athletes - needing surgery at an increasingly younger age, and with growing life expectancies, prostheses must last longer. These requirements for increased longevity and comfort raise several new challenges for doctors as well as for prosthesis manufacturers.
For manufacturers, new materials, including ceramics and metal alloys, must be evaluated and the design of prostheses must take into account various issues related to breakage, wear and noise. Doctors, on the other hand, try to mitigate the possible consequences of a micro separation between the prosthesis’ femoral head and the cavity in which it is inserted (the ‘cup’). This separation can cause micro impacts during daily use and result in premature wear.
For nearly a year the teams at ESI in France have conducted a study to help doctors and manufacturers better understand the phenomena that lead to prosthetic malfunctions. The first study was conducted to accurately simulate the kinematics and the various stresses applied on a hip prosthesis in order to understand the physics taking place in cases of extreme load, experienced in accidental cases. The teams used ESI’s integrated CAE platform, Visual-Environment to build models from geometry and material description provided by the manufacturer. They then switched to ESI’s Virtual Performance Solution to study an impact equivalent to 9K Newton in 9ms, which is representative of a severe shock, such as a patient heavily falling down the stairs. Using ESI software solutions, the study has allowed doctors and manufacturers to very accurately describe the kinematics and contact areas following a decoaptation (separation of the femoral head and cup) of the prosthesis.
A second study was conducted on behalf of a prosthesis manufacturer, Science et Médecine (SEM), based in Créteil, near Paris, France. The aim was to compare three different designs of modular prostheses fabricated from vanadium alloys, to determine which one was the most resistant in accidental cases. The precise simulation of the fitting process of the prostheses has helped SEM to accurately determine their future positioning, as well as the structural damage expected when regulatory tests are performed.
Numerical simulation is commonly used by SEM to achieve reliable design and ensure the safe use of our medical devices. We are very sensitive to software improvements, especially those incorporating dynamic simulation. The study conducted in partnership with ESI has improved our understanding of the mechanical behavior of our prostheses, for each tested design. The recent developments of simulation tools help us in increasing the reliability of medical devices including those requiring assemblies", explains Mr. Bréard, Research and Development Director, Science et Médecine.
For Fouad El-Khaldi, Industrial Strategy and Innovation Director for ESI Group, this study in the health sector is part of the company’s diversification strategy. He explains,
ESI has already proven its value in helping companies in the automotive, aerospace, energy and electronics domains. Now many other industries are turning to Virtual Prototyping as they see the benefits of being able to precertify products and anticipate product issues. Obviously, the health sector represents a huge potential market because simulation can solve customization issues and help manufacturers deliver the best solution for each and every patient, in less time and at an affordable cost.”
*Source : "Typologie et épidémiologie des prothèses totales de hanche en France", J Caton, P Papin (2012)
For more information about Virtual Performance Solution, please visit www.esi-group.com/products/virtual-performance-solution
For more ESI news, visit: www.esi-group.com/company/news
Connect with ESI on LinkedIn, Twitter, Facebook, and YouTube.
ESI Group – Media Relations
Celine.Gallerne [at] esi-group.com (Céline Gallerne)
+33 1 41 73 58 46