Worldwide
Previously, product development required iteration through numerous prototypes, proof tools, mock-ups, and pre-production builds to identify product design issues or discover challenges for assembly or maintenance workers. Interacting with products during product development escalates human factors issues or ergonomics risks that would otherwise not emerge until the Start of Production, when it is too late to resolve—due to cost, delivery timelines, quality, or safety.
Digital transformation preempts physical build with computer modeling and simulation; eliminating physical build and mock-up construction means people might not install, remove, operate, or otherwise experience the new product in the context of human-centric processes until production launch. Performing Virtual Build, Virtual Service or Maintenance, and other immersive product reviews in the context of human-centric processes, production-intent tooling, and production operators can provide similarly, and potentially better, feedback as builds with physical prototypes and mock-ups.
Our upcoming series of webinars will explore how leading enterprises effectively transcend time and space to collaborate in virtual environments. Where they experience first-hand assembly processes, product operation, and service maintenance operations weeks, months, and sometimes years before physical products are available or even advisable to produce.
Webinar Series
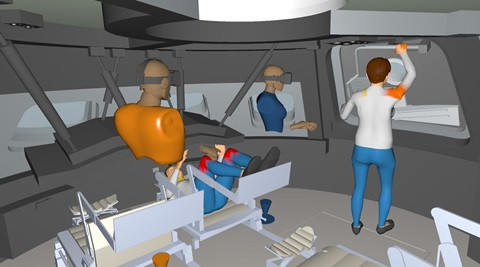
Virtual Product Design & Integration Validation|Sept 29th
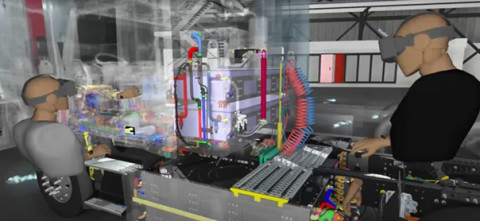
Planning for MRO Engineering Virtually I Oct 13th
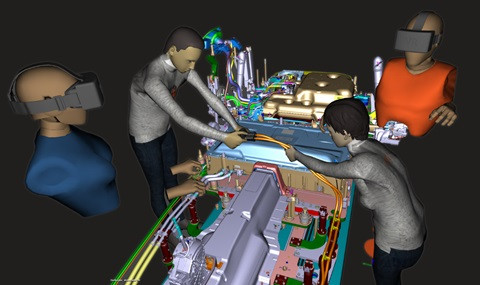
Early Assembly Process & Cell Validation Virtually I Nov 17th
Virtual Product Design & Integration Validation
Amid their industries’ digital transformations, enterprises are designing many first-of-their-kind products—Urban air-taxis, autonomous vehicles, electric drivetrains, and other disruptive product variants—that will face different problems than their historic offerings, since not all experience in producing the products of today will translate to the products of tomorrow:
- Packaging guidance defined for conventional fixed wing or rotary flight systems may exist, but will those same standards suit engineering decisions when eVTOL (electric vertical takeoff/landing) is commonplace for personal mobility?
- “Design for assembly” criteria, when available, are derived from the past century of experience with assembly practices for internal combustion vehicles, but once electrified and drivers becomes optional, would we design for assembly, service, or operation the same way?
- “Design for service” assumes we know what aspects of a design will require maintenance, but can we anticipate service for components when we don’t have statistical evidence that we are reviewing the “right processes” and do we have time to review every plausible service operation before launch?
Access the On-demand where we take a closer look at the application of Virtual and Extended reality to performing immersive product integration reviews and Design for assembly or design for service workshops.
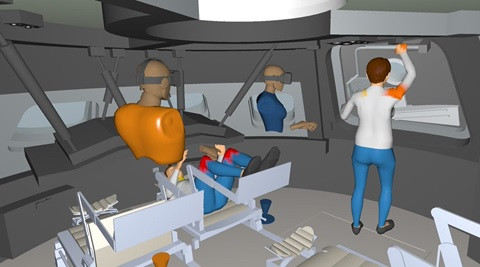
Access the On-Demand
Planning for MRO Engineering Virtually
AVAILABLE ON-DEMAND
When eXtended Reality, XR, is discussed for service and maintenance, one of the first topics that comes to mind is the use of Augmented Reality (AR) devices serving digital work instructions or real-time state reports. AR can overlay 3D views and work instructions onto real-world views, which is a tremendous value to enterprises the world over. However, where do those instructions come from and how did the authors validate them?
Conventionally, maintenance and service processes would be evaluated using pre-production prototypes and physical mock-ups constructed during product development. With digital transformation reducing or eliminating physical builds, a new risk emerges that digital work instructions defined at launch might be incomplete, create new risks, or impossible to perform. Finding out that a new product is unserviceable in the field after S.O.P., start of production, could derail an entire program and/or ground an entire fleet.
Join us Oct 13th as we look up to the addressable challenges in effective Maintenance Repair Organization planning and dig deeper into the service of long-life capital goods like aircraft and off-highway heavy machinery.
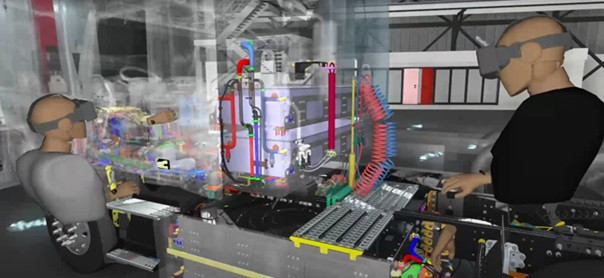
Access the On-Demand
Early Assembly Process & Cell Validation Virtually
DATE: Nov 17th
TIME: 10am CET and 11am ET (8am PT)
Manufacturing capital goods and long-life products that roll, float, or fly, that can be safely and sustainably produced, operated, and maintained by human beings is not a trivial matter. Computer-aided design tools and digital engineering methods aim to identify manufacturability constraints, predict material performance, and deterministically analyze the manufacturing requirements of the design.
However, adjacent to the products themselves, there are additional considerations like tooling, part/component logistics racks or kitting, part conveyance, and assembly cells or lines. The complexity of large-scale assembly processes is an engineering challenge as significant as designing the product itself. After all, it matters not how great a product is, when it cannot be produced sustainably.
Join us on November 17th as we discuss the virtual validation of human-performed assembly processes.
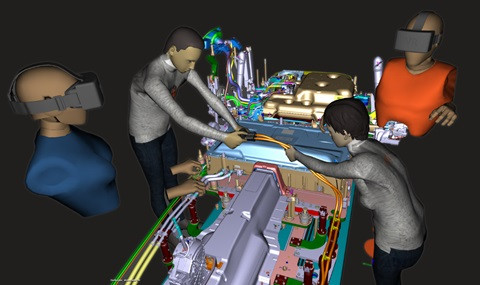
Save Your Seat
Presenter
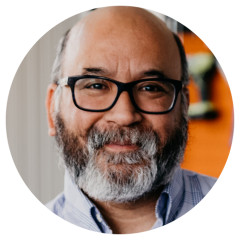