PAM-COMPOSITES
Composite Simulation Software
Composite materials, because of their lightweight properties, strength, and durability, represent key facilitators in the race to reduce carbon emissions. However, when making the shift to industrial mass production, new challenges arise with these materials:
- How to scale up production to respond to market needs?
- How to swiftly adapt to new materials to keep up with the speed of innovation in composites?
- How to price final products to meet market requirements?
Often, this calls for quick iteration and sometimes a new approach to material configuration and process parameters. Simulation allows for both.
With the unique capabilities of ESI PAM-COMPOSITES, you can study each step of the composites manufacturing chain through a process-oriented workflow. Material information and history (local shearing, local fiber content, and orientation, degree of cure, etc.), as well as geometrical properties (shape, thickness, etc.), are seamlessly transferred from one stage of the manufacturing chain to the next. This ensures maximum feedback accuracy when adjusting the process parameters to correct defects and reduce production cycle time.
Once the process chain is optimized to meet product tolerances, results are easily transferred to the design department for an “as-built” instead of “as-designed” structural analysis. This approach minimizes design margins and improves weight reduction.
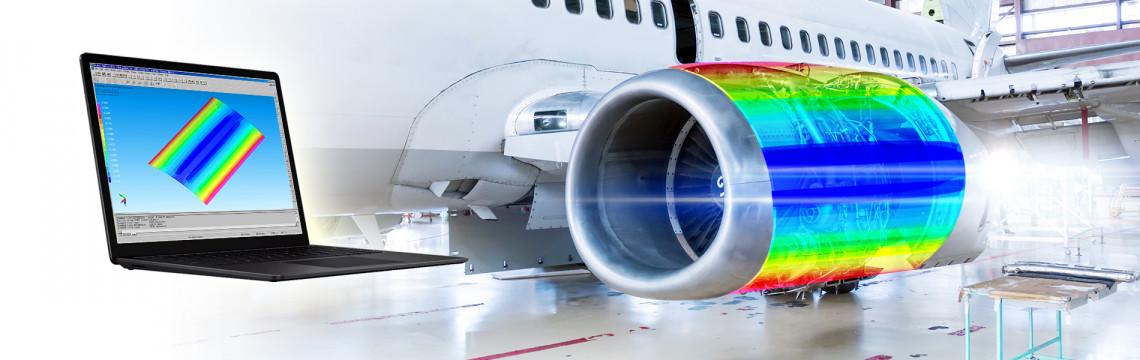
Benefits of PAM-COMPOSITES
- The only complete simulation chain on the market that can identify and fix manufacturing defects of composites products made of short, long, or continuous fibers
- Opens the door for accurate and easy determination of geometrical and material properties of “as-built” composite products, aiding design departments early in product development
- One tool that covers:
- Draping and Thermoforming
- Resin Transfer Molding (RTM), High-Pressure RTM and Compression RTM
- Resin Infusion and its variants
- Sheet Molding Compound (SMC)
- Curing and Crystallization
- Geometrical Distortions induced by the manufacturing process
- Links to CATIA by retrieving all product information defined by the design department
- Allows for a smooth transfer of manufacturing results to design departments for “as-built” structural analysis
Nissan uses Compression-RTM (C-RTM), a complex composite manufacturing process where the stamp is held partially open while the resin is injected, to reduce the time the resin takes to spread in the mold. The use of ESI PAM-COMPOSITES enabled Nissan to successfully move away from trial-and-error and redefine their C-RTM using predictive CAE by implementing a new simulation methodology. As a result, the team managed to drastically decrease manufacturing cycle time by 80%, which will support the roll-out of carbon fiber parts in lightweight vehicle mass-production.
Rieko YamaguchiVehicle Manufacturing Element Engineering Section, Vehicle Production Engineering and Development Division / Nissan
PAM-FORM, the composite forming simulation module within PAM-COMPOSITES, is used to simulate the preforming process of dry textiles or the thermoforming process of fiber-reinforced composite materials made of thermoset or thermoplastic resins (organosheets, GFRP, CFRP…).
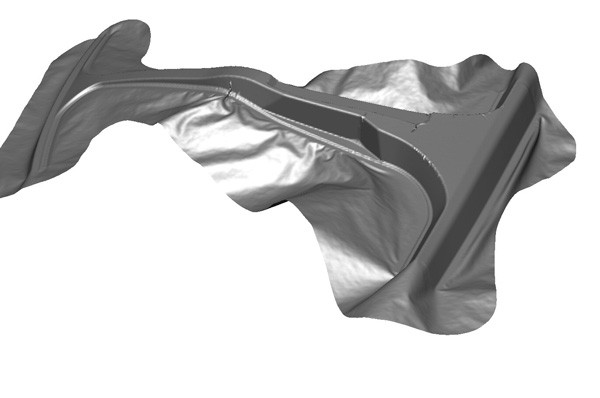
PAM-FORM allows you to model a wide range of processes including:
- stamping using two rigid molds
- rubber pad forming
- diaphragm forming
- and more
This module can be used to predict phenomena such as:
- fiber orientation
- thickness distribution
- optimum initial flat pattern
- strains
- stresses
- bridging
- wrinkling
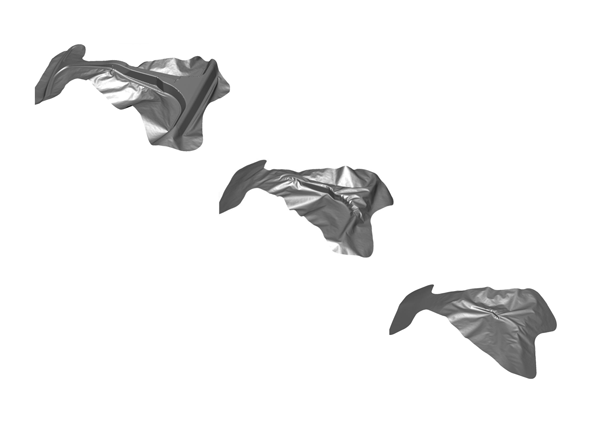
These results are available at the laminate level as well as at the ply level, allowing you to predict cases of internal wrinkles, for example, that are not visible through visual checks of physical prototypes. PAM-FORM includes material models for UniDirectional (UD), Non-Crimp Fabric (NCF), woven fabric, dry textile, thermoset prepreg, and organosheet.
With PAM-FORM, manufacturing defects are eliminated and product quality is improved upfront in the product development process, before any tools are cut, thanks to the optimization of the following process parameters:
- tool velocity
- temperature and pressure cycle
- clamping conditions and force
- laminate sequence, ply orientations
- tooling design
Simulation can also be used later in the process to correct manufacturing issues after they are identified.
PAM-RTM, the resin molding software module within PAM-COMPOSITES, is used to simulate the resin injection or the resin infusion of a preform.
PAM-RTM can model a wide range of processes including:
- Resin Transfer Molding (RTM)
- Vacuum Assisted Resin Infusion (VARI)
- Compression RTM (CRTM)
- High-Pressure RTM (HP-RTM)
- and many more
This module predicts how the resin flows in a preform that might include inserts (metals, wood, foam).
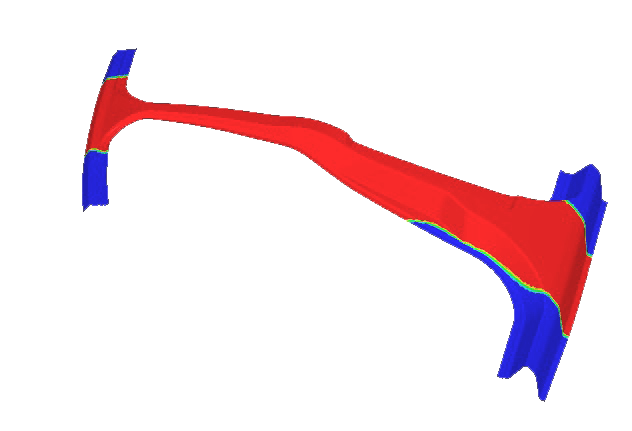
With PAM-RTM, eliminate RTM manufacturing defects, and improve product quality, upfront in the product development process, before cutting any tools, due to the optimization of the following process parameters:
- injection/infusion strategy (choice of LCM – Liquid Composite Molding - process)
- injection pressure or flow rate
- temperature cycle (tool and resin)
- location of injection gates, vents, and vacuum ports
- type and positioning of the flow media
Simulation can also be used later in the process to correct manufacturing issues after they are identified.
Typically, simulation results reveal:
- filling time
- risk of dry spots appearance or fiber washing
- flow front velocity
- pressure applied to the mold
A key parameter of Liquid Composites Molding (LCM) simulation is the permeability of the preform's reinforcements. Permeability depends highly on fiber orientations, making it essential to account for these fiber orientations in the injection/infusion process simulation. Use geometrical approaches to approximate the orientations of the fibers in the preform. However, it can also use accurate fiber orientations computed in a PAM-FORM performing simulation.
Due to its unique, high-performance DMP solver, PAM-RTM can handle large numerical models using shell or solid elements. These large numerical models are frequent in the wind industry because of the size of the components and the automotive industry because of the detailed geometry requiring small element size.
The capacity to treat very small to huge models made of solid elements is unique to PAM-RTM. This robust modeling capability is required to capture how the resin flows through the thickness and to identify risks for internal dry zones.
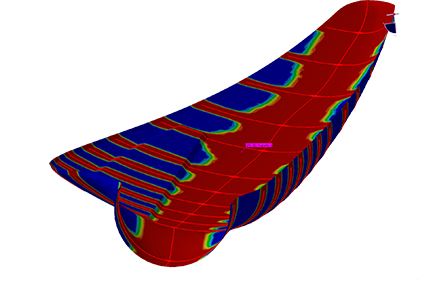
PAM-RTM's leading capabilities include:
- conditional opening and closing of the injection gates and vents
- automatic flow rate control to minimize porosities
- gravity effect
- sequential draping module for an estimate of the fiber angle in the preform
- chaining of filling and curing simulation with the possibility to include “overfilling”
- coupling with PAM-FORM and PAM-DISTORTION
- Design of Experiments (DoE) for variability analysis
ESI PAM-COMPOSITES opens the door for analysis of the curing of thermoset components, in the autoclave or out of the autoclave (OOA), and the analysis of crystallization phenomena of thermoplastic components. It also predicts, through its PAM-DISTORTION module, manufacturing-induced residual stresses and resulting geometrical distortions of produced composite parts. During manufacturing, composite parts made of thermoset matrix go through a curing operation that transforms the resin from a liquid to a solid-state. This thermo-chemical process results in residual stresses that will distort the part.
With ESI PAM-COMPOSITES, analyze the curing process, optimize the curing cycle, and predict the curing time and the evolution of the temperature and degree of cure during the cycle.
Controlling the geometrical distortion of composites parts is a critical challenge for most industries (ex. high performance aeronautic structural parts have tight tolerances). Respect of tolerances is mandatory for proper assembly and becomes vital when dealing with substantial parts such as wind blades.
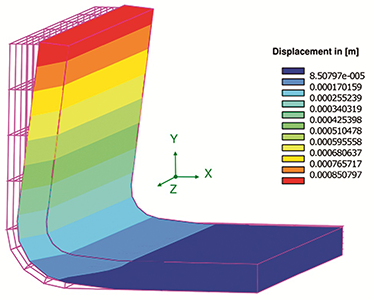
ESI PAM-COMPOSITES is an alternative to expensive and time-consuming physical trials. Prediction of manufacturing induced shape distortions makes tooling and process correction possible before trials are performed. ESI PAM-COMPOSITES computes shape distortions considering major influencing phenomena including laminate lay-up, resin thermal expansion, cure shrinkage, cure temperature, and mold thermal expansion.
Sheet Molding Compound Simulation
Sheet Molding Compound (SMC) is a multi-purpose lightweight solution, easily molded into complex shapes, allowing for the replacement of many metallic parts by one or a few SMC parts. It is a proven technology for the manufacturing of net-shape (without post operations) performant parts in large production series at a very competitive cost.
The biggest challenge with SMC is predicting and controlling local material properties of the produced part upfront in the product development process. These properties depend highly on how the fibers will reorganize (location, orientation, and density) during material compression.
To address this problem, we introduced a new module for SMC in ESI PAM-COMPOSITES 2020. This module is designed for the early design phase when engineering departments need to evaluate or iterate on new designs quickly. Since SMC material properties are so dependent on manufacturing, a simulation tool was required to help design engineers quickly and easily predict local properties.
The SMC module allows a direct link to VPS providing:
- Unique end-to-end (from manufacturing to performance) capability for SMC
- Forming and filling simulations adapted for early design (quick for multiple iterations)